Pytanie 1
Który znak umieszczony na opakowaniu informuje, że jest ono biodegradowalne?
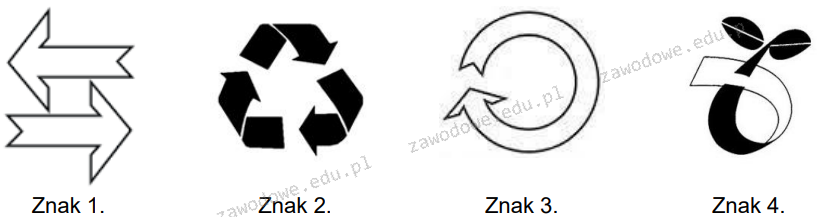
Wynik: 21/40 punktów (52,5%)
Wymagane minimum: 20 punktów (50%)
Który znak umieszczony na opakowaniu informuje, że jest ono biodegradowalne?
Który z podanych czynników nie jest wprost związany z opracowywaniem wielkości zaopatrzenia materiałowego?
W trakcie transportu środków ochrony roślin doszło do uszkodzenia opakowania. Substancja ta wdarła się do oka pracownika. Na czym polega udzielenie pierwszej pomocy poszkodowanemu?
Maksymalna wysokość ładunku na palecie (wraz z paletą EUR) nie powinna przekraczać 122 cm. Określ, ile poziomów towarów zapakowanych w kartony o wymiarach 20x20x35 cm (dł. x szer. x wys.) jest możliwe do umieszczenia na jednej palecie
Do zadań wspierających centrum dystrybucji należy
Organizowanie, monitorowanie oraz nadzorowanie zarówno dostaw surowców, jak i komponentów do produkcji, stanowi zadanie działu
Dokument, który zawiera zasady dotyczące przygotowania towaru do transportu, potencjalny zakres wymaganej kontroli, rodzaj i ilość dokumentów potrzebnych podczas przewozu, to
Do wydatków finansowych zaliczamy koszty
Jak często do centrum dystrybucji przybywają dostawy towaru A w ilości 5 000 sztuk, które są układane na paletach po 25 sztuk? Oblicz, ile ładunkowych jednostek paletowych (pjł) towaru A jest dostarczanych do centrum w skali roku?
W firmie transportowej w ciągu miesiąca przetransportowano 200 ton ładunku na łączną odległość 2 000 km. Jaka jest cena za 1 tonokilometr (tkm), jeżeli koszty transportu wyniosły 40 tys. zł?
Bezpośrednie przesyłanie informacji - dokumentów handlowych w formie elektronicznych komunikatów pomiędzy różnymi partnerami: dostawcami, producentami, odbiorcami oraz bankami - realizuje system
Naruszenie zasad BHP dotyczących ręcznego transportu ciężarów, które przekraczają ustalone limity, może prowadzić do urazów.
Harmonogramy dostaw surowców w firmie produkcyjnej są ustalane na podstawie efektywności łańcucha dostaw, który określa zdolności sprzedażowe jakiegokolwiek produktu, liczone na poziomie
Na podstawie przedstawionego cennika oblicz łączny koszt składowania przez 12 dni 20 paletowych jednostek ładunkowych i 5 kontenerów.
Cennik | ||
---|---|---|
Rodzaj jednostki ładunkowej | Składowanie jednej jednostki ładunkowej do 30 dni włącznie | Składowanie jednej jednostki ładunkowej powyżej 30 dni |
mikrojednostka | 2,50 zł/dzień | 2,00 zł/dzień |
pakietowa jednostka ładunkowa | 3,20 zł/dzień | 2,80 zł/dzień |
paletowa jednostka ładunkowa | 2,80 zł/dzień | 2,50 zł/dzień |
kontener | 32,00 zł/dzień | 29,00 zł/dzień |
W klasyfikacji XYZ litera X odnosi się do zasobów, na które istnieje zapotrzebowanie
Palety jednostkowe, heterogeniczne, składające się z różnych rodzajów towarów, w magazynach dystrybucyjnych są tworzone w obszarze
Poniższa tabela ilustruje pakiet usług logistycznych oferowanych przez
Usługi transportowe | Usługi spedycyjne | Usługi manipulacyjne (za- i wyładunek) | Usługi magazynowania | Usługi komplementacji magazynowej | Inne usługi: marketingowe informacyjne np. finansowe |
Jaką skróconą nazwę nosi kategoria systemów informatycznych wspierających zarządzanie łańcuchami dostaw, która jest wspomagana przez EDI oraz ADC?
Która metoda składowania wyróżnia się najniższym wskaźnikiem użycia przestrzeni magazynowej?
Najmniejsza jednostka produkcyjna, która potrafi działać samodzielnie, to
Huta stali w ramach optymalizacji gospodarki surowcami rozpoczęła działania mające na celu stworzenie projektu
Przedstawiony znak (białe kontury na niebieskim tle) oznacza
Dopuszczalna długość zestawu z przyczepą w większości krajów Europy wynosi
Wyznacz wartość wskaźnika rotacji zapasów w sztukach, jeśli w danym roku sprzedaż wyniosła 600 sztuk, a średni poziom zapasów wyniósł 20 sztuk?
Firma przewozowa zrealizowała usługę, za którą wystawiła fakturę na kwotę 18 450 zł brutto. Stawka VAT na usługi przewozowe wynosi 23%. Jaką kwotę netto stanowi ta usługa?
Oblicz wielkość partii produkcyjnej na podstawie przedstawionego wzoru, jeżeli czas od pobrania materiałów do zakończenia produkcji (tpz) wynosi 27 minut, czas jednostkowy wytwarzania wyrobu (tj) wynosi 0,9 godziny, a wskaźnik (q) 0,05.
n = tpz q * tj [szt.] |
W porcie kontenerowym przyjęto ładunek drobnicowy w postaci 88 palet. Jak długo potrwa rozładunek towaru, jeśli do tego zadania wykorzystano 4 wózki widłowe, a cykl transportowy jednego wózka trwa 2 minuty?
W trakcie 8-godzinnej zmiany dwójka pracowników produkuje łącznie 32 drewniane podstawy do wieszaka. Oblicz, jaka jest norma czasu pracy na toczenie jednej podstawy.
Firma zajmująca się produkcją wykorzystuje technologie produkcji opakowań zwrotnych, które oszczędzają materiały. Zakres działań, które podjęła w celu ochrony środowiska, obejmuje
System ERP w informatyce odnosi się do planowania
Zajęcie jednostek ochrony w firmie związane z potrzebami materiałowymi procesu produkcji określamy mianem
Na podstawie danych zamieszczonych w tabeli ustal, który dostawca nie zrealizował dostawy w uzgodnionym terminie.
Dostawca | Data otrzymania zamówienia | Uzgodniony termin realizacji dostawy | Data realizacji dostawy |
---|---|---|---|
A. | 01.06.2016 r. | 7 dni | 05.06.2016 r. |
B. | 12.05.2016 r. | 5 dni | 16.05.2016 r. |
C. | 24.06.2016 r. | 14 dni | 09.07.2016 r. |
D. | 25.05.2016 r. | 8 dni | 31.05.2016 r. |
Dostawcy, analizując stan zapasów u swoich klientów w oparciu o przewidywania dotyczące sprzedaży, stosują w tym celu system
Jaką maksymalną liczbę warstw ładunku o wymiarach 400 x 500 x 100 mm (dł. x szer. x wys.) i wadze 40 kg można ułożyć na palecie EUR o wymiarach 1200 x 800 x 144 mm i wadze 25 kg, biorąc pod uwagę, że maksymalna wysokość pjł. nie może wynosić więcej niż 1000 mm, a masa brutto pjł. to 800 kg, przy tym opakowań nie należy obracać?
Logistyczne centra, które oferują dostęp do infrastruktury transportowej związanej z co najmniej dwoma kategoriami transportu, to centra
Który z podanych znaków należy umieścić na opakowaniu zbiorczym z tworzywa sztucznego, zawierającym serwisy kawowe z porcelany?
System MRP odnosi się do planowania
Podane w tabeli elementy infrastruktury punktowej są charakterystyczne dla
|
|
Jeśli firma transportowa ustala koszt frachtu za usługę przewozu na podstawie tzw. opłaty stałej wynoszącej 250 zł oraz prowizji w wysokości 8% wartości ładunku, to jaki będzie koszt przewozu przy dostawie produktów o wartości 125 000 zł?
Główną cechą systemu zaopatrzenia Just in Time jest