Pytanie 1
Przedstawiony na rysunku znak, zakazuje
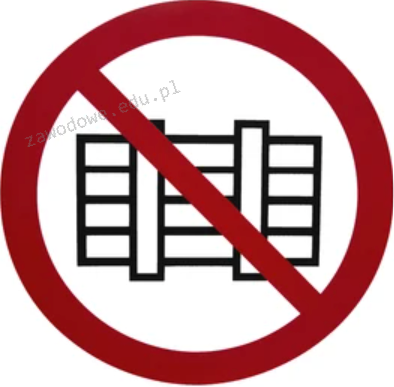
Wynik: 23/40 punktów (57,5%)
Wymagane minimum: 20 punktów (50%)
Przedstawiony na rysunku znak, zakazuje
Fazą materialną w realizacji projektu technicznego jest
W ramach operacji przygotowawczej, należy
Proces obróbki skrawaniem, w którym narzędzie obraca się, a obrabiany element porusza się w linii prostej, określa się mianem
Jakie układy w organizmie pracownika są najbardziej narażone w trakcie pracy przy linii technologicznej montażu maszyn?
W sytuacji, gdy jeden z wyłączników kontrolujących działanie prasy hydraulicznej, obsługiwanej przez dwóch pracowników, zostanie zablokowany i pozwoli na uruchomienie maszyny tylko przez jednego z nich, może to prowadzić do
Podczas ręcznego transportu ciężkich przedmiotów pracownik powinien założyć
Na mały tłok idealnej prasy hydraulicznej o średnicy 3 cm działa siła 100 N. Jaką wartość siły uzyskamy na dużym tłoku o średnicy 9 cm?
Sprawdzanie bicia promieniowego po zmontowaniu kół zębatych wykonuje się przy użyciu czujnika zegarowego na średnicy
Aby zmierzyć chropowatość powierzchni, powinno się wykorzystać
Do budowy ogrodzenia użyto stali St0S, która jest
Do metod ilościowego oszacowywania zużycia maszyn lub urządzeń technologicznych w ramach warsztatów nie zalicza się metoda
Proces obróbczy, w którym element obrabiany wykonuje ruch obrotowy, a narzędzie porusza się w kierunku posuwowym, to
Rodzaje zużycia części maszyn to stabilizowane oraz niestabilizowane
Oznaczenie Ra 6,3 na dokumencie technicznym odnosi się do
W przedstawionej poniżej fragmencie tabelki rysunku złożeniowego wynika, że na wykonanie pokrywy 805x40 należy zamówić stal
Ilość | Nazwa elementu | Poz. | Materiał | Nr normy rysunku | Nor. wymiarowa Nor. war. techn. | jedn. | całk. Masa w kg | Uwagi |
1 | Pokrywa ϕ 805×40 | 1 | 35T | rys. 97-00-0- 01-2 | PN-59/ H-84019 | 141 | 141 |
Montaż łożysk na wałkach powinien być wykonany zgodnie z odpowiednim pasowaniem?
W wyniku awarii chłodnicy w systemie hydraulicznym temperatura płynu hydraulicznego znacznie wzrosła. Praca w takich warunkach może w pierwszej kolejności prowadzić do zniszczenia
Przed pierwszym użyciem urządzenia pneumatycznego konieczne jest zweryfikowanie jego
Rodzaj połączenia, w którym następuje zmiana rozmiaru łączonych części wskutek podgrzewania lub chłodzenia jednego z nich, to połączenie
Aby zredukować luzy przed montażem, elementy należy klasyfikować na grupy w obrębie wąskich tolerancji. Opis dotyczy montażu według zasady
Który z poniższych typów przenośników kwalifikuje się jako bezcięgnowy?
Jakich substancji nie stosuje się do czyszczenia elementów maszyn przeznaczonych do montażu?
Do obsługi narzędzi oraz wyznaczania ich pozycji względem przedmiotu obrabianego wykorzystywane są
Jakiego rodzaju stal jest przeznaczona do nawęglania?
Oznaczenie "mało istotne" uszkodzenia obiektu technicznego zalicza się do
Który z elementów najsilniej wpływa na przyspieszenie procesu korozji chemicznej?
Jaką wartość ma rzeczywista wydajność pompy tłokowej o pojemności skokowej 0,1 dm3, przy prędkości obrotowej 60 obr/min, jeśli jej sprawność objętościowa wynosi 80%?
Po zakończeniu pracy na tokarce, pracownik powinien między innymi
Po umieszczeniu pierścieni na tłoku (np. silnika spalinowego), należy
Osoby pracujące przy hartowaniu elementów maszyn w cieczy solnej powinny używać odzieży ochronnej oraz
Precyzyjna obróbka ścierna przy użyciu osełek naciskanych na powierzchnię, wykorzystywana w procesie wykańczania cylindrów silników, to
Zawór, który umożliwia zmianę kierunku przepływu powietrza w systemach pneumatycznych, to:
Jakie rodzaje tworzyw sztucznych mogą być spawane w trakcie napraw?
Która z postaw ciała podczas wykonywania pracy generuje największe zmęczenie u pracownika?
Największe ryzyko uszkodzenia wzroku występuje podczas
Części maszyn, takie jak wały korbowe oraz wały rozrządu w silnikach spalinowych, są produkowane z żeliwa.
Na metalowe powierzchnie, aby zastosować powłoki ochronne przy użyciu metody galwanotechnicznej, wykorzystuje się
Podczas spawania elektrycznego konieczne jest używanie osłon oczu z uwagi na negatywne działanie promieniowania
Który z poniższych elementów przyczynia się do występowania korozji elektrochemicznej?