Pytanie 1
Który układ technologiczny magazynu przedstawiono na rysunku?
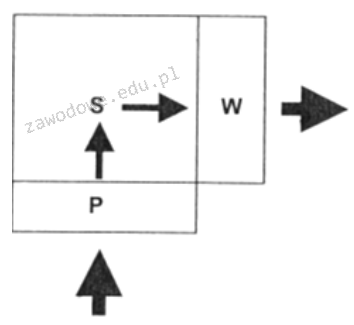
Wynik: 23/40 punktów (57,5%)
Wymagane minimum: 20 punktów (50%)
Który układ technologiczny magazynu przedstawiono na rysunku?
Firma transportowa realizuje przewozy kontenerów na trasie Gdynia-Warszawa-Gdynia. W maju 2013 roku firma poniosła koszty stałe na wszystkie zrealizowane przewozy w kwocie 4 000 zł, a koszty zmienne wyniosły 3,50 zł za 1 km. Jakie były łączne koszty na 1 km, jeśli firma zrealizowała 10 kursów w obie strony, a odległość pomiędzy Gdynią a Warszawą wynosi 400 km?
W tabeli podano korzyści użytkowania systemu informatycznego
Korzyści wynikające z użytkowania systemu informatycznego |
---|
Użytkowanie tego systemu usprawnia działanie wielu obszarów przedsiębiorstwa takich jak finanse, logistyka, produkcja, zasoby ludzkie czy obsługa klienta. Do najistotniejszych korzyści związanych z zastosowaniem tego systemu zaliczyć można: wzrost efektywności procesów gospodarczych poprzez zmniejszenie ilości zapasów oraz lepsze wykorzystanie zasobów, ulepszenie procesów zarządzania dzięki połączeniu posiadanych zasobów informacyjnych pochodzących ze wszystkich obszarów działalności oraz sprawne ich przetwarzanie, usprawnienie procesów związanych ze zbieraniem i przetwarzaniem informacji oraz wzrost poziomu ich wiarygodności oraz doskonalenie procesów logistycznych i produkcyjnych. |
Przedstawiony fragment dokumentu stanowi przykład
1. Nadawca | |||||||||||||
2. Odbiorca | 13.Przewoźnik | ||||||||||||
3. Miejsce przeznaczenia | 14. Nr rejestr. samochodu | ||||||||||||
15. Imię i nazwisko kierowcy | |||||||||||||
6. Rodzaj towaru, ilość sztuk, sposób opakowania |
A. instrukcji wysyłkowej. B. krajowego listu przewozowego. C. specyfikacji. D. zlecenia spedycyjnego. Krajowy list przewozowy to kluczowy dokument stosowany w transporcie drogowym w Polsce, który odgrywa fundamentalną rolę w zapewnieniu prawidłowego przebiegu procesu logistycznego. Jego podstawowe funkcje obejmują nie tylko potwierdzenie zawarcia umowy przewozu, ale także pełni funkcję dowodu nadania towaru oraz dokumentu niezbędnego do celów celno-skarbowych. Wypełniając krajowy list przewozowy, konieczne jest podanie szczegółowych informacji, takich jak dane nadawcy, odbiorcy, przewoźnika, a także szczegóły dotyczące towaru, w tym jego waga, objętość i rodzaj. Przykładem zastosowania krajowego listu przewozowego jest sytuacja, gdy przedsiębiorstwo transportowe dostarcza towary do klienta; dokument ten jest niezbędny do udokumentowania procesu dostawy oraz do ewentualnych roszczeń w przypadku uszkodzenia lub zagubienia towaru. Ponadto, zgodnie z ustawą o przewozie towarów, brak odpowiednio wypełnionego dokumentu może prowadzić do problemów prawnych, co podkreśla jego znaczenie w branży transportowej. Pytanie 5Zorganizowanie 30 palet, każda zawierająca 100 kartonów, przy kosztach układania 0,20 zł za karton, kosztuje A. 500 zł B. 600 zł C. 200 zł D. 300 zł Aby obliczyć całkowity koszt skompletowania 30 palet, z których każda zawiera 100 kartonów, musimy najpierw ustalić całkowitą liczbę kartonów. Mnożymy liczbę palet przez liczbę kartonów na paletę: 30 palet x 100 kartonów/paleta = 3000 kartonów. Następnie, korzystając z podanej stawki kosztu ułożenia 0,20 zł za karton, obliczamy całkowity koszt: 3000 kartonów x 0,20 zł/karton = 600 zł. Taki sposób obliczania kosztów jest zgodny z dobrymi praktykami w logistyce, gdzie kluczowe jest precyzyjne szacowanie kosztów operacyjnych. Prawidłowe określenie kosztów jest istotne dla efektywności finansowej firmy oraz podejmowania decyzji o alokacji zasobów. Przykładem może być zastosowanie tej metody w magazynowaniu, gdzie znajomość kosztów związanego z pakowaniem i przechowywaniem towarów wpływa na cenę końcową produktów i rentowność działalności. Pytanie 6To pytanie jest dostępne tylko dla zalogowanych użytkowników. Zaloguj się lub utwórz konto aby zobaczyć pełną treść pytania. Odpowiedzi dostępne po zalogowaniu. Wyjaśnienie dostępne po zalogowaniu. Pytanie 7Który z poniższych systemów pozwala na dostarczanie w czasie rzeczywistym aktualnych danych dotyczących bieżącej produkcji oraz różnic pomiędzy planowanymi a uzyskanymi wskaźnikami produkcji? A. Wytwarzanie wspomagane komputerowo. B. Zarządzanie relacjami z klientami. C. System realizacji produkcji. D. Planowanie potrzeb materiałowych. Systemy Customer Relationship Management (CRM) koncentrują się na zarządzaniu relacjami z klientami, co obejmuje zbieranie danych o klientach, analizowanie ich potrzeb oraz wspieranie sprzedaży. Choć ważne, nie są one ukierunkowane na monitorowanie produkcji ani rozbieżności w procesach wytwórczych. Z kolei Material Requirements Planning (MRP) to system, który planuje zapotrzebowanie materiałowe na podstawie prognoz sprzedaży i zamówień. MRP koncentruje się głównie na tym, co i kiedy zamówić, aby zaspokoić zapotrzebowanie, ale nie śledzi bieżącej wydajności produkcji ani nie dostarcza informacji w czasie rzeczywistym. Computer Aided Manufacturing (CAM) wspiera procesy wytwórcze, automatyzując zadania związane z obróbką materiałów, jednak nie jest to system zaprojektowany do monitorowania i analizowania produkcji jako całości. Wybór niewłaściwego systemu często wynika z błędnego zrozumienia ich funkcji oraz z pominięcia kontekstu, w jakim są one stosowane. Kluczowe jest, aby przy wyborze narzędzi informatycznych kierować się ich specyfiką i przeznaczeniem, co pozwala unikać dezorientacji i efektywnie zarządzać procesami produkcyjnymi. Pytanie 8Wybór środka transportu, zabezpieczenie ładunku oraz przygotowanie dokumentacji przewozowej to działania A. zarządzające zachodzące w trakcie procesu transportowego B. zarządzające odbywające się przed przewozem C. operacyjne mające miejsce przed przewozem D. operacyjne realizowane w trakcie procesu transportowego Wybór odpowiedzi sugerujących, że czynności te są wykonawcze występujące w trakcie procesu transportowego lub organizacyjne występujące w jego trakcie, prowadzi do nieporozumienia dotyczącego etapów procesu transportowego. Proces transportowy dzieli się na kilka kluczowych etapów: organizację, realizację oraz kontrolę. Czynności takie jak wybór środka transportu, ubezpieczenie ładunku oraz sporządzanie dokumentów przewozowych są częścią etapu organizacyjnego, który ma miejsce przed samym przewozem. W praktyce, działania wykonawcze odnosiłyby się do czynności, które są realizowane już w trakcie dostarczania towaru, takie jak załadunek, transport czy rozładunek. Pominięcie znaczenia etapu organizacyjnego może prowadzić do nieefektywnych decyzji, takich jak niewłaściwy wybór środka transportu, co może skutkować opóźnieniami, dodatkowymi kosztami lub problemami z bezpieczeństwem ładunku. Koncentracja na organizacji przed przewozem jest kluczowa dla osiągnięcia sukcesu w operacjach logistycznych i transportowych. Właściwe przygotowania przyczyniają się do płynności całego procesu, a także pomagają w zapewnieniu zgodności z przepisami prawa, co jest niezbędne w każdej branży transportowej. Pytanie 9To pytanie jest dostępne tylko dla zalogowanych użytkowników. Zaloguj się lub utwórz konto aby zobaczyć pełną treść pytania. Odpowiedzi dostępne po zalogowaniu. Wyjaśnienie dostępne po zalogowaniu. Pytanie 10Ewidencjonowanie przekazania surowców z magazynu do działu produkcji odbywa się za pomocą dokumentu A. PZ B. RW C. WZ D. MM Odpowiedź RW jest prawidłowa, ponieważ dokument RW (Rozchód Wewnętrzny) jest używany do ewidencjonowania przekazywania surowców z magazynu do produkcji. Ten dokument odzwierciedla proces, w którym materiały są wydawane z magazynu i przesyłane do działu produkcji, co jest kluczowe dla prawidłowego zarządzania zapasami i zapewnienia ciągłości procesu produkcyjnego. W praktyce, za pomocą dokumentu RW można dokładnie kontrolować ilość wydawanych surowców, co pozwala na monitorowanie stanu magazynowego oraz planowanie dalszych dostaw. Zgodnie z dobrymi praktykami w zarządzaniu magazynami, każde wydanie surowców powinno być dokładnie dokumentowane, aby uniknąć błędów w ewidencji oraz zapewnić zgodność z normami finansowymi i podatkowymi. Ponadto, prawidłowe wykorzystanie dokumentu RW wspiera analizę kosztów produkcji, umożliwiając przedsiębiorstwom lepsze podejmowanie decyzji strategicznych w zakresie optymalizacji procesów produkcyjnych i zarządzania zapasami. Pytanie 11Pracownik magazynu otrzymał listę pozycji asortymentowych oraz ilości towarów do pobrania, a także pick by light w celu A. konfekcjonowania zamówienia B. kompletowania zamówienia C. przyjęcia i rozmieszczenia towaru D. ułożenia jednostek ładunkowych Wybór odpowiedzi dotyczącej konfekcjonowania zamówienia jest błędny, ponieważ konfekcjonowanie odnosi się do procesu pakowania i przygotowywania towarów do wysyłki, a nie bezpośrednio do ich zbierania z magazynu. Często mylone jest pojęcie kompletacji z konfekcjonowaniem, co prowadzi do nieporozumień związanych z tym, jakie czynności są realizowane w danym etapie procesów magazynowych. Podobnie, odpowiedzi sugerujące przyjęcie i rozmieszczenie towaru, czy ułożenie jednostek ładunkowych, pomijają kluczowe różnice pomiędzy tymi procesami a kompletowaniem zamówienia. Przyjęcie towaru to proces związany z weryfikacją i rejestracją produktów przybywających do magazynu, co nie ma związku z ich zbieraniem na potrzeby zamówień. Ułożenie jednostek ładunkowych natomiast dotyczy optymalizacji przestrzeni magazynowej i organizacji towarów, a nie ich wydawania. Ważne jest, aby w kontekście zarządzania magazynem rozróżniać poszczególne etapy, ponieważ każdy z nich wiąże się z innymi procedurami i standardami operacyjnymi, co ma istotne znaczenie dla efektywności całego procesu logistycznego. Zrozumienie tych różnic pozwala na lepsze zarządzanie zapasami oraz zwiększa efektywność operacyjną, a także zadowolenie klientów. Pytanie 12Dokument, który dokumentuje przekazanie surowców do produkcji, to A. rozchód wewnętrzny B. zwrot wewnętrzny C. przesunięcie międzymagazynowe D. wydanie z magazynu Wybór odpowiedzi wydanie z magazynu, zwrot wewnętrzny oraz przesunięcie międzymagazynowe jest nieprawidłowy, ponieważ każde z tych pojęć odnosi się do różnych aspektów zarządzania materiałami i nie odzwierciedla w pełni procesu przekazywania materiałów do produkcji. Wydanie z magazynu to dokument, który zazwyczaj oznacza, że materiały są wydawane z magazynu do konkretnego odbiorcy zewnętrznego lub wewnętrznego, ale niekoniecznie wiąże się to bezpośrednio z ich użyciem w produkcji. Może się zdarzyć, że materiały wydane z magazynu nie zostaną wykorzystane natychmiast w produkcie końcowym. Z kolei zwrot wewnętrzny dotyczy sytuacji, w której materiały, które wcześniej zostały wydane, są zwracane z powrotem do magazynu, co również nie jest zgodne z procesem ich przekazywania do produkcji. Przesunięcie międzymagazynowe odnosi się do transferu towarów pomiędzy różnymi lokalizacjami magazynowymi, co również nie jest równoznaczne z ich wykorzystaniem w procesie wytwarzania. Te pojęcia mogą prowadzić do nieporozumień, jeśli nie zostaną właściwie zdefiniowane w kontekście zarządzania łańcuchem dostaw oraz produkcji, co jest kluczowe dla osiągnięcia efektywności operacyjnej w każdej organizacji. Właściwe zrozumienie terminologii i dokumentacji związanej z gospodarką magazynową jest niezbędne dla skutecznego zarządzania procesami, co jest ważne nie tylko dla skuteczności produkcji, ale również dla poprawy rentowności przedsiębiorstwa. Pytanie 13Opakowania, które zostały wykorzystane, są A. ubocznymi produktami działań produkcyjnych i usługowych. B. towarami odrzuconymi. C. ubocznymi produktami procesów wydobywczych. D. resztkami po spożyciu. Zużyte opakowania, określane jako pozostałości pokonsumpcyjne, są to odpady, które powstają w wyniku konsumpcji produktów. Z perspektywy zarządzania odpadami, ich prawidłowa klasyfikacja jest kluczowa dla efektywnego recyklingu oraz zmniejszenia wpływu na środowisko. Przykładami takich opakowań są butelki po napojach, kartony po mleku czy opakowania po jedzeniu. W kontekście dobrych praktyk, wiele krajów wdraża systemy segregacji, które ułatwiają przetwarzanie tych odpadów. Standardy takie jak ISO 14001 promują zarządzanie odpadami w sposób zrównoważony, co sprzyja ochronie środowiska. Edukacja społeczeństwa na temat znaczenia recyklingu oraz odpowiedzialnego gospodarowania odpadami jest niezbędna dla osiągnięcia celów zrównoważonego rozwoju. Prawidłowe podejście do pozostałości pokonsumpcyjnych pozwala na ich skuteczne przetworzenie, a tym samym ograniczenie potrzeby wydobycia surowców pierwotnych. Pytanie 14Na podstawie analizy wymagań sieci dystrybucji można stwierdzić, że: A. 700 szt. B. 100 szt. C. 250 szt. D. 950 szt. Aby obliczyć zapas dysponowany w sieci dystrybucji, należy uwzględnić zarówno zapas początkowy, sprzedane jednostki, jak i dostawy. Wyliczenie przeprowadza się za pomocą wzoru: Zapas dysponowany = Zapas początkowy + Dostawy - Sprzedaż. W podanym przypadku, mamy: Zapas dysponowany = 2250 + 250 - 1550 = 950 szt. Taka kalkulacja jest fundamentalna w zarządzaniu łańcuchem dostaw, ponieważ pozwala na bieżąco monitorować stan magazynu i podejmować decyzje dotyczące uzupełnienia zapasów. W praktyce, zrozumienie dynamiki zapasów jest kluczowe dla efektywności operacyjnej. Na przykład, wiedząc, że zapas dysponowany wynosi 950 sztuk, manager ds. logistyki może odpowiednio zaplanować przyszłe zamówienia, aby uniknąć braków i niepotrzebnych kosztów związanych z nadmiernym magazynowaniem. Dobrym standardem jest regularne analizowanie zapasów w kontekście sprzedaży i prognozowania, co pozwala na optymalizację zarządzania zapasami oraz poprawę zadowolenia klientów przez zapewnienie dostępności produktów. Pytanie 15Firma zajmująca się transportem otrzymała zlecenie na przewóz ładunku do czterech odbiorców: A. IV, III, I, II B. II, III, I, IV C. IV, I, III, II D. I, II, III, IV Wybór innych sekwencji dostaw nie uwzględnia kluczowych zasad optymalizacji transportu. Na przykład, sekwencja II, III, I, IV ignoruje priorytet cięższych ładunków, co prowadzi do nieefektywnego wykorzystania przestrzeni ładunkowej. Zaczynając od odbiorcy II, który ma najmniejszy ładunek (0,5 tony), transport jest nieefektywnie wypełniony, co zwiększa liczbę kursów i tym samym koszty operacyjne. Kolejność IV, III, I, II również nie jest optymalna, ponieważ dostarczanie najpierw do odbiorcy IV (2 tony) po kolejnych mniejszych ładunkach prowadzi do niekonsekwentnego zarządzania przestrzenią ładunkową. Selekcja I, II, III, IV jest także niekorzystna, ponieważ największy ładunek (2 tony) jest przewożony na końcu, co oznacza, że początkowo pojazd mógłby być niewykorzystany w pełni, zwiększając całkowity czas transportu. Typowym błędem w takich sytuacjach jest koncentrowanie się na kolejności dostaw według odbiorców, a nie na efektywności ładunku. To prowadzi do wydłużenia czasu dostawy oraz zwiększenia kosztów paliwa. Z perspektywy najlepszych praktyk branżowych kluczowe jest, aby planować dostawy na podstawie wielkości ładunków oraz dystansu, co zapewnia maksymalizację efektywności operacyjnej. Pytanie 16Jaką metodę ustalania ilości dostaw powinno się wybrać przy bardzo dużych wydatkach na magazynowanie, niskich kosztach transportu oraz ekstremalnie krótkim czasie realizacji zamówienia? A. Stałej częstotliwości dostawy B. Maksymalnej dostawy C. Partia na partię D. Stałej wielkości dostawy Odpowiedź 'Partia na partię' jest prawidłowa, gdyż ta metoda dostosowuje się do okoliczności, w których koszty magazynowania są znaczne, a koszty dostawy są stosunkowo niskie. W tym modelu dostaw zamówienia realizowane są w małych partiach w odpowiedzi na bieżące zapotrzebowanie, co minimalizuje koszty przechowywania oraz pozwala na elastyczne reagowanie na zmiany w popycie. Przykładem praktycznym może być branża spożywcza, gdzie świeże produkty są dostarczane na bieżąco, co ogranicza konieczność długoterminowego magazynowania i zmniejsza ryzyko przeterminowania. Ta metoda jest zgodna z dobrymi praktykami, które zalecają optymalizację procesów dostaw w celu zminimalizowania kosztów i zwiększenia efektywności operacyjnej. Dobrze zorganizowany system dostaw oparty na tej metodzie pozwala na utrzymanie konkurencyjności i zadowolenia klientów. Pytanie 17O ergonomii wózka widłowego, nabytego do transportu elektrycznego, świadczy przede wszystkim to, że pojazd zapewnia A. długotrwałe użytkowanie, pełny serwis po upływie okresu gwarancyjnego B. łatwe wsiadanie i wysiadanie z pojazdu oraz zamkniętą, ogrzewaną kabinę C. osiągnięcie kompromisu między wydajnością a niskim zużyciem energii D. szybką i stabilną pracę w trudnych warunkach Wybór opcji dotyczącej łatwego wsiadania i wysiadania z wózka oraz zabudowanej, ogrzewanej kabiny jako wskaźnika ergonomiczności wózka widłowego jest uzasadniony z kilku powodów. Ergonomia w kontekście wózków widłowych odnosi się do projektowania tych urządzeń w taki sposób, aby maksymalizować komfort i efektywność pracy operatora. Łatwe wsiadanie i wysiadanie z wózka zmniejsza ryzyko kontuzji, co jest szczególnie istotne przy długotrwałym użytkowaniu. Ergonomicznie zaprojektowane kabiny zapewniają odpowiednią przestrzeń, co pozwala operatorowi na swobodne poruszanie się. Dodatkowo, zabudowana, ogrzewana kabina jest istotna w trudnych warunkach atmosferycznych, co wpływa na komfort pracy i zwiększa wydajność. W kontekście standardów branżowych, takie podejście do projektowania wózków widłowych jest zgodne z zasadami ergonomii pracy, które mają na celu redukcję zmęczenia i poprawę bezpieczeństwa operatorów. W praktyce, odpowiednia ergonomia przekłada się na mniejsze ryzyko wystąpienia urazów, co również wpływa na efektywność operacyjną i obniżenie kosztów eksploatacji. Pytanie 18Zbiór działań realizowanych przez wyznaczoną grupę pracowników, których celem jest zapewnienie klientom dostępu do produktów w odpowiedniej jakości, ilości, miejscu oraz czasie, odbywa się w obrębie A. produkcji B. magazynowania C. dystrybucji D. zaopatrzenia Wybór odpowiedzi 'dystrybucji' jest trafny, ponieważ dystrybucja to proces, który polega na zarządzaniu przepływem towarów od producenta do ostatecznego konsumenta. Obejmuje szereg działań, takich jak transport, magazynowanie, zarządzanie zapasami i dostarczanie produktów do lokalnych punktów sprzedaży. Kluczowym celem dystrybucji jest zapewnienie, że towary są dostępne dla klientów w odpowiednim czasie, jakości i ilości. Przykładem skutecznej dystrybucji mogą być sieci detaliczne, które optymalizują swoje łańcuchy dostaw, aby zminimalizować czas dostawy i zredukować koszty transportu. Standardy takie jak ISO 9001 w zarządzaniu jakością oraz praktyki Lean i Just-In-Time są często stosowane w celu poprawy efektywności procesów dystrybucyjnych. Dzięki tym standardom, organizacje mogą dostosować swoje działania do wymagań rynkowych oraz potrzeb klientów, co przekłada się na wyższą satysfakcję klientów oraz zyski organizacji. Pytanie 19Wydatki związane z zatrudnieniem pracowników w magazynie oraz amortyzacją sprzętu magazynowego są klasyfikowane jako koszty A. niedoboru zapasów B. uzupełniania zapasów C. utrzymania zapasów D. przesycenia zapasami Wybór odpowiedzi związanej z nadmiarem zapasów wskazuje na nieporozumienie dotyczące klasyfikacji kosztów w kontekście zarządzania magazynem. Koszty nadmiaru zapasów dotyczą sytuacji, w której przedsiębiorstwo posiada zbyt duże ilości towarów, co może prowadzić do problemów finansowych, jak np. zwiększone koszty przechowywania czy ryzyko przestarzałości produktów. Utrzymanie zapasów, w przeciwieństwie do nadmiaru zapasów, skupia się na wydatkach związanych z efektywnym zarządzaniem posiadanymi zapasami i zapewnieniu ich dostępności. Odnosząc się do braku zapasów, można zauważyć, że koszty te dotyczą utraty sprzedaży i potencjalnych niezadowolonych klientów, co również jest inną kategorią wydatków. Uzupełnianie zapasów odnosi się do działań mających na celu przywrócenie poziomu zapasów do optymalnego stanu, co wiąże się z innymi kosztami, takimi jak zamówienia i transport. Właściwe zrozumienie różnicy pomiędzy tymi pojęciami jest kluczowe dla efektywnego zarządzania zapasami oraz minimalizacji kosztów w organizacji. Dlatego istotne jest, aby nie mylić tych kategorii kosztów, gdyż mogą one prowadzić do nieadekwatnych strategii finansowych i operacyjnych. Pytanie 20Firma określiła zapas łożysk na poziomie 1 000 sztuk. Aktualny stan magazynowy łożysk wynosi 1 840 sztuk, a dzienne zużycie to 280 sztuk. Po jakim czasie firma powinna złożyć zamówienie na łożyska? A. Za 5 dni B. Za 6 dni C. Za 10 dni D. Za 3 dni Poprawna odpowiedź to 3 dni, ponieważ przedsiębiorstwo posiada 1 840 sztuk łożysk, a zapas informacyjny wynosi 1 000 sztuk. Różnica, która pokazuje nadwyżkę, to 1 840 - 1 000 = 840 sztuk. Dzienne zużycie łożysk wynosi 280 sztuk, co oznacza, że 840 sztuk wystarczy na 840 / 280 = 3 dni. W praktyce, przedsiębiorstwa często ustalają zapasy informacyjne, aby zabezpieczyć się przed ewentualnymi opóźnieniami w dostawach lub wzrostem popytu. Uwzględnienie zapasu informacyjnego w obliczeniach pozwala na efektywniejsze zarządzanie stanami magazynowymi i minimalizację ryzyka przestojów w produkcji. Standardem w branży jest stosowanie odpowiednich wskaźników i prognoz, które pomagają w ustalaniu optymalnych poziomów zapasów, co ma kluczowe znaczenie dla dalszego rozwoju i stabilności przedsiębiorstwa. Pytanie 21Jakie wyroby charakteryzują się dystrybucją intensywną? A. Nabiał B. Telewizor C. Meble D. Samochód Odpowiedź "Nabiał" jest poprawna, ponieważ towary dystrybuowane intensywnie charakteryzują się szeroką dostępnością oraz częstym zakupem przez konsumentów. Nabiał, jako produkt codziennego użytku, musi być dostępny w dużych ilościach w supermarketach i sklepach spożywczych, aby zaspokoić popyt klientów. Standardy dystrybucji intensywnej zakładają minimalizację kosztów i maksymalizację dostępności, co jest szczególnie istotne w przypadku produktów szybko psujących się, takich jak mleko czy jogurty. W praktyce oznacza to, że producenci nabiału często współpracują z dużymi sieciami handlowymi, aby zapewnić regularne dostawy i wysoką rotację towarów. Przy odpowiednim zarządzaniu łańcuchem dostaw, można efektywnie redukować straty oraz zwiększać efektywność operacyjną. Dobrym przykładem jest strategia Just-in-Time, która pozwala na minimalizację zapasów i jednoczesne utrzymanie wysokiej dostępności produktów na półkach. W branży spożywczej, dbanie o odpowiednie warunki przechowywania i transportu nabiału jest kluczowe dla jakości oraz bezpieczeństwa żywności. Pytanie 22W ciągu miesiąca (30 dni) magazyn poniósł stałe wydatki w wysokości 45 000,00 zł oraz zmienne wydatki w wysokości 75 000,00 zł. Jaka jest dzienna jednostkowa kwota kosztów magazynowania zapasu, jeśli w magazynie średnio znajduje się 20 000 szt. zapasu? A. 0,20 zł B. 2,25 zł C. 6,00 zł D. 0,13 zł Wiesz, co jest ważne przy obliczaniu dziennego kosztu magazynowania? Trzeba brać pod uwagę zarówno koszty stałe, jak i zmienne. Więc w naszym przypadku mamy 45 000 zł na koszty stałe i 75 000 zł na zmienne. Jak to zsumujemy, to wychodzi 120 000 zł w miesiącu. Teraz, żeby obliczyć koszt na dzień, dzielimy to przez 30 dni, co daje nam 4 000 zł. Potem musimy jeszcze podzielić to przez średnią liczbę zapasów w magazynie, czyli 20 000 sztuk. I co dostajemy? Równe 0,20 zł na sztukę dziennie. Takie podejście jest zgodne z dobrymi praktykami. Dzięki temu lepiej zarządza się zapasami i przy okazji można lepiej ustalać ceny. Moim zdaniem, zrozumienie tych kosztów naprawdę pomaga w podejmowaniu lepszych decyzji. Pytanie 23Który magazyn oferuje najniższy koszt wyładunku i składowania 12 t ładunku przez 7 dni (tydzień)?
A. Magazyn III. B. Magazyn II. C. Magazyn IV. D. Magazyn I. Analiza kosztów wyładunku i składowania 12 ton ładunku przez 7 dni w różnych magazynach może wydawać się skomplikowana, jednak kluczowe jest zrozumienie, dlaczego wybór innego magazynu może prowadzić do błędnych wniosków. Wybierając Magazyn I, II lub III, można popełnić kilka podstawowych błędów myślowych. Po pierwsze, błędna analiza kosztów może wynikać z niepełnych informacji o stawkach, które mogą różnić się w zależności od długości przechowywania lub ilości ładunku. Każdy z tych magazynów mógłby oferować atrakcyjne stawki wyładunku, jednak suma kosztów za całą operację jest kluczowa. Dodatkowo, brak znajomości standardów efektywności operacyjnej, takich jak zarządzanie przestrzenią czy logistyka wewnętrzna, może prowadzić do wyboru opcji, która na pierwszy rzut oka wydaje się korzystna, ale w rzeczywistości generuje wyższe koszty. Warto także zrozumieć, że koszty składowania mogą być zróżnicowane w zależności od lokalizacji magazynu, dostępności usług dodatkowych oraz jakości obsługi klienta. Inwestowanie w odpowiednią infrastrukturę i technologie, jak automatizacja procesów magazynowych, może przynieść długofalowe oszczędności i poprawić efektywność. Dlatego zawsze warto analizować różne aspekty operacyjne i nie opierać się wyłącznie na pojedynczych danych kosztowych, co może prowadzić do nietrafnych wyborów w logistyce. Pytanie 24Jakie są korzyści z implementacji automatycznego systemu zarządzania informacją w procesie składowania? A. redukcja efektywności i produktywności magazynu B. wzrost wydatków w łańcuchu dostaw C. usprawnienie obsługi klientów D. zmniejszenie dostępności asortymentu Odpowiedzi, które sugerują zwiększenie kosztów w łańcuchu dostaw, ograniczenie dostępności asortymentu, czy zmniejszenie wydajności magazynu, są oparte na błędnych założeniach dotyczących funkcji automatyzacji w logistyce. W rzeczywistości, wdrożenie zautomatyzowanego systemu przepływu informacji powinno prowadzić do obniżenia kosztów operacyjnych w łańcuchu dostaw, poprzez optymalizację procesów, co jest zgodne z najlepszymi praktykami w branży. Automatyzacja zmniejsza potrzebę ręcznego wprowadzania danych, co minimalizuje ryzyko błędów oraz związane z nimi koszty. Ograniczenie dostępności asortymentu jest również nieuzasadnione, ponieważ automatyzacja sprzyja dokładniejszemu zarządzaniu zapasami i lepszemu prognozowaniu, co w efekcie zwiększa dostępność produktów. Ponadto, zautomatyzowane systemy mają na celu poprawę wydajności i produktywności magazynu, co jest kluczowe dla utrzymania konkurencyjności na rynku. Niewłaściwe interpretacje tych procesów mogą prowadzić do błędnych wniosków, takich jak przekonanie, że automatyzacja wiąże się z większymi kosztami lub obniżoną jakością obsługi klienta, co jest sprzeczne z danymi z badań i projektów wdrożeniowych, które pokazują, że automatyzacja w rzeczywistości podnosi standardy i efektywność operacyjną. Pytanie 25Określ właściwą sekwencję działań w procesie analizy łańcucha dostaw. A. Analiza i prognozowanie -> planowanie sieci i łańcuchów dostaw -> przepływ produktów w łańcuchu dostaw B. Analiza i prognozowanie -> przepływ produktów w łańcuchu dostaw -> planowanie sieci i łańcuchów dostaw C. Planowanie sieci i łańcuchów dostaw -> analiza i prognozowanie -> przepływ produktów w łańcuchu dostaw D. Przepływ produktów w łańcuchu dostaw -> planowanie sieci i łańcuchów dostaw -> analiza i prognozowanie Odpowiedź wskazująca na kolejność: analiza i prognozowanie -> planowanie sieci i łańcuchów dostaw -> przepływ produktów w sieci dostaw jest prawidłowa, ponieważ każdy z tych kroków jest od siebie zależny i niezbędny w skutecznym zarządzaniu łańcuchem dostaw. Na etapie analizy i prognozowania zbierane są dane dotyczące popytu, dostępności surowców oraz trendów rynkowych, co pozwala na podejmowanie świadomych decyzji. Następnie, na podstawie tych analiz, następuje planowanie sieci dostaw, które obejmuje lokalizację magazynów, wybór dostawców oraz ustalenie tras transportowych. Dzięki właściwie rozplanowanej sieci, przepływ produktów staje się bardziej efektywny, co przekłada się na obniżenie kosztów i skrócenie czasu dostaw. Przykładowo, firmy korzystające z narzędzi takich jak SAP APO czy Oracle SCM potrafią w sposób zintegrowany zarządzać tymi procesami, co stanowi standard w branży. Efektywna analiza, planowanie oraz zarządzanie przepływem produktów to kluczowe elementy, które przyczyniają się do osiągnięcia przewagi konkurencyjnej na rynku. Pytanie 26Informatycznym systemem wspierającym zarządzanie, nadzór oraz kontrolowanie przepływu towarów w magazynie, a także mającym na celu udostępnianie informacji o tym procesie i generowanie dokumentacji związanej z tym przepływem jest A. WMS B. MRP I C. EDI D. SCM WMS, czyli System Zarządzania Magazynem, jest kluczowym narzędziem w logistyce, które wspiera organizację i kontrolę procesów magazynowych. Jego zadaniem jest optymalizacja przepływu towarów w magazynie, co obejmuje zarówno przyjmowanie, składowanie, jak i wydawanie produktów. Dzięki WMS, przedsiębiorstwa mogą uzyskać dokładne informacje o stanie zapasów w czasie rzeczywistym, co pozwala na podejmowanie szybkich i świadomych decyzji. Przykładowo, WMS umożliwia automatyzację procesów, takich jak kompletacja zamówień, co z kolei przyczynia się do zwiększenia efektywności operacyjnej. W branży e-commerce, gdzie czas dostawy ma kluczowe znaczenie, wdrożenie WMS może znacząco poprawić zadowolenie klientów. Dobre praktyki dotyczące wdrażania WMS obejmują przeszkolenie personelu, integrację systemu z innymi rozwiązaniami IT oraz regularne aktualizacje, aby system pozostał zgodny z najnowszymi standardami branżowymi. Pytanie 27To pytanie jest dostępne tylko dla zalogowanych użytkowników. Zaloguj się lub utwórz konto aby zobaczyć pełną treść pytania. Odpowiedzi dostępne po zalogowaniu. Wyjaśnienie dostępne po zalogowaniu. Pytanie 28W magazynie przed przyjęciem znajdowało się 1 500 szt. towaru, a po przyjęciu 17 500 szt. Oblicz, jaka jest wartość średniego zapasu cyklicznego w tym magazynie, jeśli stanowi ona połowę wartości dostawy? A. 750 szt. B. 9 000 szt. C. 8 750 szt. D. 8 000 szt. Błędne odpowiedzi pojawiają się często z powodu niepełnego zrozumienia tego, czym jest średni zapas cykliczny i jak się go oblicza. Wielu uczniów myśli, że oblicza się go na podstawie zapasu przed dostawą lub po dostawie, a to nie do końca tak działa. Trzeba pamiętać, że dostawa to różnica między stanem magazynowym przed i po dostawie. Tutaj w sumie wychodzi 16 000 sztuk dostawy, więc średni zapas cykliczny jako połowa tej wartości to 8 000 sztuk. Jeśli zrozumiesz te zasady, to będzie ci łatwiej planować i prognozować w logistyce, bo niewłaściwa ilość zapasów może naprawdę podnieść koszty i prowadzić do braków towarowych. Pytanie 29W magazynie, jaką zasadę składowania określa metoda rotacji zapasów? A. przydzieleniu produktom stałych lokalizacji magazynowych B. kategoryzowaniu towarów według częstotliwości ich wydania C. podziale ładunków w oparciu o ich masę D. lokowaniu towarów w miejscach, gdzie jest dostępna przestrzeń Odpowiedź dotycząca grupowania towarów na podstawie częstotliwości pobrań jest zgodna z zasadami rotacji zapasów, które są kluczowe dla efektywnego zarządzania magazynem. Metoda ta, często określana jako zasada ABC, polega na analizie danych dotyczących ruchu towarów i klasyfikacji ich według częstotliwości pobrań. Towary, które są najczęściej pobierane, są umieszczane w łatwo dostępnych miejscach, co znacznie skraca czas kompletacji zamówień. Przykładowo, w magazynie, gdzie sprzedawane są artykuły spożywcze, najczęściej kupowane produkty, takie jak napoje czy przekąski, powinny być umiejscowione na poziomie oczu, aby pracownicy mogli je szybko zlokalizować. Tego rodzaju rotacja zapasów nie tylko poprawia efektywność operacyjną, ale również wpływa na zadowolenie klientów, którzy otrzymują zamówienia szybciej. Warto również zwrócić uwagę na standardy takie jak Lean Management, które podkreślają eliminację marnotrawstwa i optymalizację procesów magazynowych, co jest w pełni zgodne z metodą rotacji zapasów. Pytanie 30W przedsiębiorstwie logistycznym, w procesie magazynowania można wyróżnić etapy jego realizacji, które określają następujące obszary funkcjonalne? A. przygotowania, przyjęcia, składowania, wysyłki B. przyjęcia, przygotowania zamówienia, wysyłki, składowania C. składowania, przyjęcia, przygotowania zamówienia, wysyłki D. przyjęcia, składowania, przygotowania zamówienia, wysyłki Odpowiedzi, które nie uwzględniają wszystkich kluczowych faz procesu magazynowania, mogą prowadzić do niepełnego zrozumienia mechanizmów operacyjnych w firmach logistycznych. Wiele z tych odpowiedzi pomija istotne etapy, takie jak faza przygotowania, co jest kluczowe przed przyjęciem towarów do magazynu. W praktyce, przygotowanie towarów obejmuje różne działania, takie jak sprawdzenie dokumentacji transportowej oraz organizację przestrzeni magazynowej. Pominięcie tego etapu może prowadzić do chaosu w przyjęciach i błędów w dokumentacji. Dodatkowo, niektóre odpowiedzi zamieniają kolejność faz, co może wpływać na skuteczność operacji magazynowych oraz na czas realizacji zamówień. Przykładem błędnego podejścia jest skupienie się wyłącznie na składowaniu i wysyłce, co należy traktować jako końcowe etapy procesu, a nie podstawowe. Takie myślenie pomija kluczowe aspekty planowania i organizacji, które są fundamentalne dla sukcesu w logistyce. W praktyce, przyjęcia i przygotowanie zamówienia są ściśle ze sobą powiązane i nie mogą funkcjonować w izolacji, ponieważ błędy na etapie przygotowania mogą wpływać na efektywność całego procesu magazynowania i dystrybucji. Pytanie 31To pytanie jest dostępne tylko dla zalogowanych użytkowników. Zaloguj się lub utwórz konto aby zobaczyć pełną treść pytania. Odpowiedzi dostępne po zalogowaniu. Wyjaśnienie dostępne po zalogowaniu. Pytanie 32Ułożenie ładunków bezpośrednio na podłodze, gdzie stosy zorganizowano w rzędach lub blokach, znajduje zastosowanie w magazynach A. wielopoziomowych B. niskich C. specjalistycznych D. wysokich Jak się ma do magazynów niskich, to fajnie, że ładunki można kłaść prosto na podłodze. To naprawdę pozwala lepiej wykorzystać przestrzeń, bo w takich magazynach wysokość nie jest jakoś specjalnie duża, do 4 metrów. Z własnego doświadczenia widzę, że najlepiej sprawdza się układ blokowy – palety poukładane w rzędach to jest to! Dzięki temu widać dokładnie, co gdzie leży, a dostęp do towarów jest znacznie lepszy. No i tak jak w normach ISO piszą, to wszystko prowadzi do większej wydajności w magazynowaniu. Po prostu, jak można znaleźć bardziej sensowny sposób na rozmieszczenie towarów, to warto z tego skorzystać. Ułożenie jednostek ładunkowych bezpośrednio na posadzce to na pewno dobry wybór w takich przypadkach. Pytanie 33Zastosowanie wielkości obrotu towarowego podczas planowania układu towarów w magazynie ma na celu A. skrócenie odległości przemieszczania towarów w magazynie B. zapewnienie stałych miejsc do transportu towarów C. uproszczenie procesu kompletacji zamawianych towarów D. wyszukiwanie dostępnych miejsc do transportu towarów Planowanie rozmieszczenia towarów w magazynie z uwzględnieniem wielkości obrotu ma na celu nie tylko poprawę efektywności, ale także skuteczne zarządzanie przestrzenią magazynową. Utrzymywanie stałych miejsc transportu towarów to podejście, które niekoniecznie sprzyja elastyczności i skuteczności operacyjnej. W praktyce, stałe przypisanie towarów do konkretnych lokalizacji może prowadzić do dłuższego czasu skanowania i pobierania produktów, co nie jest optymalne w kontekście zmiennych potrzeb rynku. Z kolei wyszukiwanie wolnych miejsc transportu może być mylące, ponieważ efektywne rozmieszczenie towarów powinno opierać się na ich rotacji, a nie na dostępności przestrzeni. Uproszczenie kompletacji zamawianego towaru, mimo że ważne, nie wystarczy samo w sobie; kluczowe jest, aby te działania były zgodne z zasadami efektywnego zarządzania zapasami oraz rozważania przestrzenne. Powszechnym błędem jest zakładanie, że samo przypisanie towaru do wyznaczonej lokalizacji wystarczy, aby zminimalizować koszty i czas operacji. W rzeczywistości, odpowiednie rozmieszczenie towarów powinno opierać się na ich charakterystyce, rotacji oraz sezonowości, co wymaga analizy danych i elastyczności w zarządzaniu. Dobre praktyki sugerują, że optymalizacja w magazynie powinna być dynamiczna, z uwzględnieniem zmieniających się potrzeb i obrotów, co prowadzi do zwiększenia wydajności i niskich kosztów operacyjnych. Pytanie 34To pytanie jest dostępne tylko dla zalogowanych użytkowników. Zaloguj się lub utwórz konto aby zobaczyć pełną treść pytania. Odpowiedzi dostępne po zalogowaniu. Wyjaśnienie dostępne po zalogowaniu. Pytanie 35Jeśli całkowite koszty składowania w analizowanym okresie wynoszą 8000 zł, a wartość obrotu magazynowego według wydania w tym czasie to 2000 szt., jaki jest wskaźnik kosztów składowania? A. 16 zł/szt. B. 2 zł/szt. C. 4 zł/szt. D. 8 zł/szt. Odpowiedź 4 zł/szt. jest prawidłowa, ponieważ wskaźnik kosztów magazynowania oblicza się, dzieląc łączne koszty magazynowania przez wielkość obrotu magazynowego. W tym przypadku mamy 8000 zł jako łączne koszty magazynowania oraz 2000 sztuk jako wielkość obrotu. Zatem obliczenie wygląda następująco: 8000 zł / 2000 szt. = 4 zł/szt. Taki wskaźnik jest kluczowy dla zarządzania kosztami w logistyce, pozwala firmom monitorować efektywność zarządzania magazynem oraz planować przyszłe inwestycje w infrastrukturę magazynową. W praktyce, znajomość tego wskaźnika pozwala na optymalizację procesów magazynowych, takich jak zarządzanie zapasami czy analiza kosztów. Analizując wskaźnik kosztów magazynowania, można zauważyć, że jego zmniejszenie może prowadzić do poprawy rentowności firmy, co jest zgodne z dobrą praktyką branżową dotyczącą efektywności operacyjnej. Pytanie 36Naruszenie zasad BHP dotyczących ręcznego transportu ciężarów, które przekraczają ustalone limity, może prowadzić do urazów. A. kończyn górnych B. kończyn dolnych C. kręgosłupa D. głowy Nieprzestrzeganie przepisów BHP podczas ręcznego przemieszczania ciężarów o masie przekraczającej ustalone normy rzeczywiście może prowadzić do poważnych urazów, w szczególności kręgosłupa. Kręgosłup jest strukturą anatomiczną, która jest szczególnie narażona na przeciążenia, szczególnie gdy ciężar jest źle podnoszony lub przenoszony. Właściwe techniki podnoszenia, takie jak utrzymywanie ciężaru blisko ciała oraz uginanie kolan zamiast pleców, są kluczowe w zapobieganiu urazom. W standardach BHP, takich jak normy PN-N-18002 oraz PN-N-18001, podkreśla się znaczenie szkoleń w zakresie ergonomii i bezpieczeństwa pracy. Przykładowo, pracownicy magazynów powinni być regularnie szkoleni w zakresie technik bezpiecznego podnoszenia. Mity dotyczące podnoszenia ciężarów, takie jak przekonanie, że można podnosić ciężkie przedmioty bez odpowiedniego przygotowania, mogą prowadzić do poważnych problemów zdrowotnych, w tym przewlekłych bóli pleców i urazów kręgosłupa. Pytanie 37Do zadań centrów logistycznych należy między innymi A. pobudzanie działalności gospodarczej oraz przyciąganie inwestorów, maksymalizacja zysków B. świadczenie kompleksowych usług oraz zapewnienie elastyczności konfigurowania łańcucha dostaw C. ograniczanie negatywnego wpływu przewozu ładunków na środowisko, maksymalizacja zysków D. elastyczność w zakresie konfigurowania łańcucha dostaw, monopolizacja rynku Wybierając inne odpowiedzi, można napotkać na szereg nieporozumień dotyczących roli centrów logistycznych. Wiele z nich koncentruje się na aspektach, które są tylko częściowo związane z ich rzeczywistymi funkcjami. Na przykład, założenie, że centra logistyczne mają na celu maksymalizację zysków, może prowadzić do uproszczenia postrzegania ich działalności. W rzeczywistości ich głównym celem jest optymalizacja procesów, co w rezultacie może prowadzić do zwiększenia rentowności, ale nie jest to ich podstawowa misja. Również koncepcja monopolizacji rynku jest mylna, ponieważ centra logistyczne konkurują na rynkach lokalnych i globalnych, co sprzyja innowacyjności i poprawie jakości usług. Z kolei zmniejszanie uciążliwości środowiskowej przewozu ładunków, choć ważne w kontekście zrównoważonego rozwoju, nie jest bezpośrednim celem centrów logistycznych. Ich zadania obejmują przede wszystkim koordynację i zarządzanie przepływem towarów, co wpływa zarówno na ekonomię, jak i na środowisko, ale nie można tego mylić z priorytetowym dążeniem do minimalizacji wpływu na środowisko. Kluczowym błędem myślowym jest przypisywanie centrów logistycznych roli, która wykracza poza ich rzeczywiste funkcje i odpowiedzialności, co może prowadzić do dezinformacji na temat ich wpływu na gospodarkę i środowisko. Pytanie 38Głównym zamiarem udzielania pierwszej pomocy nie jest A. przygotowanie do dalszej interwencji medycznej B. minimalizacja skutków urazów lub choroby C. ratowanie życia ludzkiego D. obniżenie wydatków na odszkodowanie Głównym celem udzielania pierwszej pomocy jest ochrona życia ludzkiego oraz ograniczenie skutków obrażeń lub choroby. Przygotowanie do dalszego postępowania lekarskiego również stanowi istotny element, ale nie może być traktowane jako główny cel. Przykładem jest sytuacja, gdy osoba ulega wypadkowi – ratownik najpierw zabezpiecza podstawowe funkcje życiowe poszkodowanego, takie jak oddech i krążenie, zanim przekaże go w ręce specjalistów medycznych. Osoby udzielające pierwszej pomocy powinny kierować się wytycznymi międzynarodowych organizacji zdrowotnych, takich jak Europejska Rada Resuscytacji, które postulują, że każda interwencja ma na celu ratowanie życia i minimalizowanie dalszych uszkodzeń. W praktyce, umiejętność szybkiego reagowania i stosowania podstawowych technik, jak resuscytacja krążeniowo-oddechowa (RKO) czy zabezpieczenie urazów, jest kluczowa dla poprawy rokowań pacjenta. Pytanie 39Na początku miesiąca w magazynie firmy zajmującej się produkcją odzieży stwierdzono zapas 5000 metrów materiału. W trakcie miesiąca zakupiono dodatkowo 2500 metrów materiału. Minimalny zapas konieczny do zapewnienia ciągłości produkcji wynosi 6000 metrów. Jaką wartość ma zapas nadwyżkowy? A. 2500 m B. 1000 m C. 1500 m D. 3500 m Odpowiedzi, które nie wskazują na 1500 metrów, ignorują kluczowy aspekt obliczeń dotyczących zarządzania zapasami. Na przykład, odpowiedzi sugerujące 1000 metrów lub 2500 metrów nie uwzględniają całkowitego stanu zapasów po zakupach oraz nie dostrzegają, że zapas bieżący musi być zgodny z wymaganiami produkcyjnymi. Istotnym błędem w myśleniu jest zaniżanie zapasu nadmiernego poprzez niepełne uwzględnienie zakupów. Obliczanie zapasu nadmiernego powinno zawsze bazować na rzeczywistym stanie zapasów, a nie na subiektywnych osądach co do tego, ile materiału jest potrzebne. Ponadto, odpowiedzi, które wynoszą 3500 metrów, mylnie zakładają, że zapas bieżący powinien być większy niż zapas całkowity, co jest sprzeczne z zasadą efektywności operacyjnej. W praktyce, błędne obliczenia mogą prowadzić do nadmiernych kosztów operacyjnych oraz niewłaściwego wykorzystania zasobów, co w dłuższej perspektywie negatywnie wpływa na rentowność przedsiębiorstwa. Dlatego istotne jest, aby w procesie podejmowania decyzji związanych z zarządzaniem zapasami, bazować na precyzyjnych obliczeniach oraz analizować dane zgodnie z najlepszymi praktykami i standardami branżowymi. Pytanie 40Sklep detaliczny nabył towar w hurtowni, która na swój koszt i odpowiedzialność zobowiązała się dostarczyć go do magazynu kupującego. Jaką formułę zastosował dostawca? A. Franco magazyn dostawcy B. Loco magazyn dostawcy C. Loco magazyn odbiorcy D. Franco magazyn odbiorcy Odpowiedź 'Franco magazyn odbiorcy' jest poprawna, ponieważ oznacza, że sprzedający ponosi wszystkie koszty i ryzyko związane z dostarczeniem towarów do miejsca wskazanego przez nabywcę, w tym przypadku do magazynu odbiorcy. Taki mechanizm jest zgodny z zasadami Incoterms, które regulują warunki dostaw w handlu międzynarodowym. Przykładem zastosowania tej formuły może być sytuacja, w której producent towarów w Polsce sprzedaje je detalistom w Niemczech. Producent organizuje transport i pokrywa koszty dostawy do magazynu detalisty. Dzięki temu detalista nie musi martwić się o logistykę dostawy, co ułatwia mu prowadzenie działalności. Praktyka ta jest szczególnie korzystna dla nabywców, którzy mogą skupić się na sprzedaży i obsłudze klienta, mając pewność, że towary dotrą na czas i w dobrym stanie. Warto również zauważyć, że stosowanie formuły 'Franco' sprzyja przejrzystości kosztów w transakcjach handlowych, co jest istotne dla planowania finansowego przedsiębiorstw. |