Pytanie 1
Przedstawiony na rysunku znak umieszczony na opakowaniu oznacza
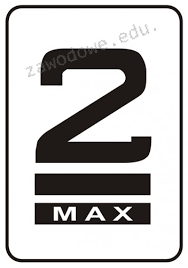
Wynik: 29/40 punktów (72,5%)
Wymagane minimum: 20 punktów (50%)
Przedstawiony na rysunku znak umieszczony na opakowaniu oznacza
Wszystkie drogi ewakuacyjne w budynkach użyteczności publicznej są oznakowane. Przedstawiony znak oznacza kierunek drogi ewakuacyjnej schodami
Jaką zasadę reprezentuje metoda FIFO?
Realizacja procesu wytwórczego dla produktu końcowego, który nie był dotąd produkowany, na podstawie zamówienia klienta, stanowi zaopatrzenie materiałowe do produkcji
Na podstawie załączonego cennika ustal, jaką opłatę pobierze terminal za składowanie jednego pełnego kontenera 40ft przez okres 8 dni.
KONTENERY | J.m. | Pełne | Puste | |||
---|---|---|---|---|---|---|
20ft | 40ft | 20ft | 40ft | |||
1. | Sztauerka statkowa | szt. | 264,00 | 343,00 | 176,00 | 232,00 |
2. | Przeładunek burta-plac lub odwrotnie | szt. | 123,00 | 160,00 | 89,00 | 115,00 |
3. | Przeładunek plac-samochód/wagon lub odwrotnie | szt. | 123,00 | 160,00 | 89,00 | 115,00 |
4. | Opłata bezpieczeństwa (ISPS) | szt. | 7,40 | 7,40 | - | - |
5. | Manipulacja | szt. | 253,00 | 329,00 | 253,00 | 329,00 |
Składowanie: | ||||||
6. | 7 dni wliczone w stawkę przeładunkową | - | - | - | - | - |
7. | Od 8 do 14 dnia | szt./dzień | 10,70 | 21,40 | 10,70 | 21,40 |
8. | Od 15 do 21 dnia | szt./dzień | 21,40 | 43,40 | 21,40 | 43,40 |
9. | Od 22 do 28 dnia | szt./dzień | 27,50 | 54,60 | 27,50 | 54,60 |
10. | Od 29 dnia | szt./dzień | 47,40 | 95,00 | 47,40 | 95,00 |
Stawki taryfy wyrażone są w złotych polskich. |
Jaki wtórny dokument magazynowy umożliwia rejestrację zapasów firmy w jednostkach fizycznych oraz finansowych?
Przedstawiona nalepka umieszczona na opakowaniu oznacza
Wyznacz wskaźnik zaspokojenia potrzeb zapasem, jeżeli przeciętny miesięczny popyt na towar wynosi 1 200 szt., a przeciętny stan zapasów to 600 szt.
Roczne wydatki na zatrudnienie pracowników w magazynie wynoszą 84 000 zł. Zazwyczaj w tym miejscu pracuje 6 osób. Jaki jest wskaźnik kosztów jednostkowych zatrudnienia, który umożliwia zaplanowanie budżetu na następny rok?
Firma logistyczna ma dostarczyć ładunek do czterech odbiorców, w kolejności: X, Y, Z, L jednym środkiem transportu. Czas dowozu zamówionego ładunku od dostawcy do odbiorcy X oraz powrót samochodu od odbiorcy L do bazy wynosi po 30 minut. Łączny czas pracy kierowcy wynosi
Trasa | Odległości | Prędkość pojazdu na trasie | Czas rozładunku |
---|---|---|---|
Odbiorca X-Y | 120 km | 60 km/h | 20 min. |
Odbiorca Y-Z | 60 km | 60 km/h | 20 min. |
Odbiorca Z-I | 180 km | 60 km/h | 20 min. |
Brak odpowiedzi na to pytanie.
Jaki układ technologiczny magazynu przedstawiono na schemacie?
W każdym z procesów logistycznych działania związane z realizowaniem zamówień definiuje plan
Jaką minimalną liczbę stanowisk z owijarką do palet powinno się przewidzieć w magazynie działającym przez 16 godzin dziennie, gdzie planowane jest zabezpieczenie 960 paletowych jednostek ładunkowych (pjł) w ciągu doby, a średni czas obsługi jednej pjł przez owijarkę wynosi 5 minut?
Jak nazywa się system informatyczny, który służy do synchronizacji działań oraz planowania przepływu materiałów w całym łańcuchu dostaw, oznaczany skrótem?
Wybrane standardy jakości owoców i warzyw do obrotu hurtowego zgodne z wymaganiami klientów Która dostawa nie spełnia gentlemenS agreements co do wielkości zepsutych produktów?
Partia jest zgodna ze standardem, gdy więcej niż 90% zawartości wszystkich opakowań spełnia wymagania:
Zgodnie z gentlemen's agreement (dżentelmeńska umowa) dopuszcza się u klienta do 2% zepsutych owoców i warzyw. |
Wykaz zrealizowanych dostaw
Masa zepsutych produktów [kg] | Wielkość dostawy | |
---|---|---|
Dostawa 1. | 22 | 40 skrzyń jabłek po 25 kg jabłek w skrzyni |
Dostawa 2. | 10 | 80 worków z ziemniakami po 50 kg ziemniaków w worku |
Dostawa 3. | 31 | 4 pjł z kapustą pekińską po 600 kg kapusty na palecie |
Dostawa 4. | 54 | 240 kartonów z pomidorami po 15 kg pomidorów w kartonie |
System organizacji dostaw materiałów w procesie produkcyjnym, oparty na przekazywaniu informacji o potrzebie zainicjowania przepływu materiałów, zapisanej na tzw. karcie to
Czym kierujemy się przy ustalaniu optymalnej partii zakupów?
Które urządzenie jest przedstawione na ilustracji?
Gdy zużycie pewnych dóbr zmienia się, a prognozy są obarczone błędami, to w celu uniknięcia braku w zapasie utrzymujemy zapas
Międzynarodowy dokument przewozowy CMR oznacza zawarcie umowy dotyczącej transportu towarów w formie
W przedsiębiorstwie poziom zapasu rotacyjnego zależy
Który wózek przeznaczony jest do przewozu beczki?
Zakład przyjął zamówienie na 96 sztuk głowic do silników. Produkcja zamówionych głowic na jednej linii produkcyjnej w jednej zmianie dziennie zajmie 48 dni. Ile dni potrwa produkcja, jeśli zostanie uruchomiona druga linia produkcyjna, a prace na obu liniach będą prowadzone na trzech zmianach?
Wykorzystanie strategii Just in Time (czyli dokładnie na czas) pozwala między innymi na zarządzanie
Na którym rysunku przedstawiono kontener IBC (Intermediate Bulk Container)?
Aby chronić się przed oczekiwanymi wzrostami cen, tworzy się zapas
Na ilustracji jest przedstawiony wózek do obsługi
Która z metod zarządzania zapasami umożliwia firmom produkcyjnym utrzymanie stanów magazynowych bliskich zera?
Przedstawione na rysunku wypełnienie kartonu ma na celu
Przeniesienie ładunku do pojazdu o mniejszej ładowności to
Jakie zestawienie pokazuje właściwą sekwencję procesów w łańcuchu dostaw?
Które opakowanie powinno zostać wybrane do przechowywania 120 sztuk wyrobów gotowych o wymiarach 55 x 35 x 14 cm (długość x szerokość x wysokość), jeżeli wyroby w opakowaniu mają być piętrzone w 3 warstwach i przechowywane w pionie?
Opakowanie 1. | Opakowanie 2. | Opakowanie 3. | Opakowanie 4. |
---|---|---|---|
– długość: 600 mm – szerokość: 320 mm – wysokość: 500 mm – w magazynie: 20 szt. | – długość: 600 mm – szerokość: 400 mm – wysokość: 500 mm – w magazynie: 50 szt. | – długość: 600 mm – szerokość: 350 mm – wysokość: 150 mm – w magazynie: 40 szt. | – długość: 600 mm – szerokość: 320 mm – wysokość: 400 mm – w magazynie: 10 szt. |
B. | C. | D. |
Brak odpowiedzi na to pytanie.
Badanie analizy ABC dotyczącej zapasów w magazynie w celu ich właściwego rozmieszczenia w strefie składowania, mającego na celu zredukowanie czasu operacji manipulacyjnych, realizowane jest na podstawie kryterium
Jakie jest podstawowe zadanie systemu WMS?
W firmie zajmującej się produkcją, która działa 200 dni w roku, roczna sprzedaż wyniosła 8 000 sztuk. Średni stan zapasów w tym okresie wynosił 400 sztuk. Jak obliczyć wskaźnik rotacji zapasów?
Brak odpowiedzi na to pytanie.
Gdzie w procesie rozdzielania zapasów znajdują się najbliżej klienta?
Zdefiniuj ilość towarów znajdujących się w firmie lub w łańcuchu dostaw, które nie są aktualnie wykorzystywane, ale są przeznaczone do dalszego przetworzenia lub sprzedaży, jako
Jeśli do centrum dystrybucji realizowane są zamówienia produktów w ilości 12 000 sztuk, 4 razy w miesiącu, to roczny wolumen dostaw wynosi
Kod kreskowy EAN-13 wykorzystujemy do identyfikacji opakowań przy pomocy numeru GTIN
Który z poniższych towarów zostanie wprowadzony do systemu dystrybucji selektywnej?