Pytanie 1
Na ilustracji jest przedstawione rozmieszczenie w magazynie grup zapasów wydzielonych na podstawie analizy ABC sporządzonej według kryterium
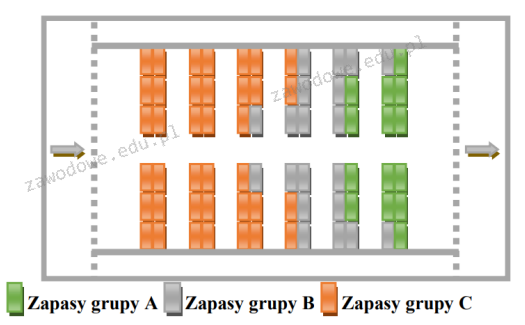
Wynik: 13/40 punktów (32,5%)
Wymagane minimum: 20 punktów (50%)
Na ilustracji jest przedstawione rozmieszczenie w magazynie grup zapasów wydzielonych na podstawie analizy ABC sporządzonej według kryterium
Strategia selektywnej dystrybucji jest wykorzystywana podczas sprzedaży towarów
Który karton został poprawnie odłożony na regał magazynowy uwzględniając umieszczony na nim znak manipulacyjny?
Skrót, który odnosi się do systemu informacyjnego wspierającego procesy związane z rozmieszczaniem towarów w magazynach oraz zarządzaniem tymi magazynami, to
Działania planowane, których konsekwencje zauważalne są w krótkim czasie, określamy mianem planowania
Po pozytywnym zakończeniu audytu systemu zarządzania jakością, firma transportowa otrzymuje
Metoda opierająca się na założeniu, że zapotrzebowanie w nadchodzącym okresie pozostanie identyczne jak w okresie wcześniejszym, nosi nazwę
Przedstawiony znak oznacza materiały i przedmioty
Dla artykułów, których długość znacząco przewyższa inne wymiary gabarytowe i wynosi więcej niż 1,2 m, tworzy się jednostki ładunkowe
Na podstawie danych zawartych w tabeli ustal ekonomiczną wielkość dostawy.
Wielkość dostawy [kg] | Koszt utrzymania zapasu [zł] | Koszt uzupełniania zapasu [zł] | Całkowity koszt utrzymania i uzupełniania zapasu [zł] |
---|---|---|---|
75 | 260,00 | 185,00 | 445,00 |
50 | 240,00 | 160,00 | 400,00 |
25 | 195,00 | 195,00 | 390,00 |
10 | 170,00 | 240,00 | 410,00 |
Etykieta logistyczna GS1 ma na celu identyfikację jednostki logistycznej dla uczestników łańcucha dostaw. Jedyną informacją obowiązkową, która musi się znaleźć na każdej etykiecie logistycznej, niezależnie od tego, czy dotyczy palet jednorodnych, niejednorodnych, standardowych czy niestandardowych, jest
Do jakich kosztów przypisuje się wydatki na utrzymanie magazynu?
Procedury, które należy stosować w przypadku pożaru, powinny być opisane w
Przykładem opakowania, które służy do tworzenia jednostek ładunkowych w magazynach oraz podczas transportu, jest
Które urządzenie nie służy bezpośrednio do identyfikacji towarów, a jest jedynie urządzeniem wspomagającym automatyczną identyfikację?
Całkowite wydatki na przechowywanie towarów w danym czasie wyniosły 8 000 zł, a wartość obrotu magazynowego obliczona na podstawie rozchodu osiągnęła 2 000 szt. Jaki jest koszt jednostkowy przechowywania towarów?
Na ilustracji jest przedstawiona kontrola jakości dostawy towarów przeprowadzana metodą
Na podstawie danych zawartych w tabeli ustal czas, potrzebny na montaż szafki.
Operacja | Całkowity czas przygotowawczo-zakończeniowy [h] | Liczba operacji na wyrób [szt.] | Jednostkowy czas wykonania operacji [h] |
---|---|---|---|
Przykręcenie boków do dolnej podstawy szafki | 0,4 | 2 | 0,2 |
Przykręcenie boków do górnej podstawy szafki | 0,4 | 2 | 0,2 |
Przymocowanie tylnej płyty | 0,3 | 1 | 0,1 |
To pytanie jest dostępne tylko dla zalogowanych użytkowników. Zaloguj się lub utwórz konto aby zobaczyć pełną treść pytania.
Odpowiedzi dostępne po zalogowaniu.
Wyjaśnienie dostępne po zalogowaniu.
Pracownik magazynu otrzymał wykaz pozycji asortymentowych oraz ilości do pobrania wraz z pick by light w celu
To pytanie jest dostępne tylko dla zalogowanych użytkowników. Zaloguj się lub utwórz konto aby zobaczyć pełną treść pytania.
Odpowiedzi dostępne po zalogowaniu.
Wyjaśnienie dostępne po zalogowaniu.
Skrót, którym określane są systemy informatyczne używane do automatycznego zbierania i wprowadzania danych, to
Na którym rysunku przedstawiono kontener IBC (Intermediate Bulk Container)?
Informatyczny system używany do kontrolowania obiegu zapasów w magazynie to
Korzystając z kartoteki magazynowej zamieszczonej w tabeli, określ wartość rozchodu towaru wydanego na podstawie dokumentu RW 24 stosując do wyceny metodę FIFO.
Lp. | Data | Symbol i nr dokumentu | Jednostkowa cena zakupu netto [zł] | Ilość [szt.] | ||
---|---|---|---|---|---|---|
Przychód | Rozchód | Zapas | ||||
1. | 12.06.2018 | --- | 4,00 | --- | --- | 1 200 |
2. | 13.06.2018 | PZ 13 | 4,50 | 3 200 | --- | 4 400 |
3. | 15.06.2018 | PZ 14 | 5,00 | 2 500 | --- | 6 900 |
4. | 18.06.2018 | RW 24 | 5 500 |
To pytanie jest dostępne tylko dla zalogowanych użytkowników. Zaloguj się lub utwórz konto aby zobaczyć pełną treść pytania.
Odpowiedzi dostępne po zalogowaniu.
Wyjaśnienie dostępne po zalogowaniu.
W I kwartale firma logistyczna poniosła wydatki na zatrudnienie 100 pracowników w wysokości 120 000 zł. W II kwartale planowany jest spadek liczby pracowników o 20%. Przy założeniu, że łączne koszty zatrudnienia nie ulegną obniżeniu, ile wyniesie średni koszt zatrudnienia 1 pracownika w II kwartale?
Koncepcja, w ramach której towary dostarczone do terminala, niemal bez składowania, są natychmiast sortowane, dzielone na mniejsze partie, a po połączeniu z innymi towarami są przekazywane do różnych odbiorców, nazywana jest
Na rysunku przedstawiono dystrybucję towarów w systemie
Aby wyprodukować zaplanowane 500 sztuk skrzyń, potrzebne są 250 m2 płyty. Dotychczas wydano 100 m2 płyty, a dodatkowe 100 m2 płyty jest w magazynie. Ile jeszcze płyty należy zamówić, aby zrealizować planowaną produkcję?
Zarządzanie procesem odzyskiwania produktów obejmuje wszystkie wymienione poniżej działania:
Zjawiska zachodzące w ramach całej gospodarki narodowej określamy jako
System, który oferuje elektroniczną bazę danych do wymiany standardowych dokumentów, to
Który z poniższych składników nie jest zintegrowany z elektronicznym systemem oprogramowania, który umożliwia całościowe zarządzanie dokumentami oraz procesami pracy w dystrybucji?
Brak odpowiedzi na to pytanie.
Jeśli 480 zamówień zostało zrealizowanych prawidłowo, a 20 zamówień okazało się niekompletnych, to jaki procent dostaw jest kompletny?
Brak odpowiedzi na to pytanie.
Wartość brutto sprzedanych towarów zgodnie z przedstawioną fakturą wynosi
Brak odpowiedzi na to pytanie.
Termin dostarczenia zamówienia ustalono na 10 dzień miesiąca. W którym dniu powinno się złożyć zamówienie, jeśli czas realizacji dostawy wynosi 4 dni?
Brak odpowiedzi na to pytanie.
Jakie działania wchodzą w skład funkcji logistycznych realizowanych w centrum logistycznym?
Brak odpowiedzi na to pytanie.
Tabela przedstawia wartość przesyłek doręczonych przez przedsiębiorstwo kurierskie w roku 2011. W analizie statystycznej zjawiska posłużono się wskaźnikiem
Rodzaj przesyłki | Wartość przesyłki w zł | Udział w % |
---|---|---|
zwykłe | 57 500 | 57,5 |
ekspresowe | 42 500 | 42,5 |
Razem | 100 000 | 100,0 |
Brak odpowiedzi na to pytanie.
Ile paletowych jednostek uda się załadować w ciągu pięciu dni, jeżeli magazyn funkcjonuje na trzech zmianach, a podczas jednej zmiany wydawanych i załadowanych na środki transportu jest średnio 320 pjł?
Brak odpowiedzi na to pytanie.