Pytanie 1
Ile wynosi wartość zapasu nieprawidłowego na podstawie przedstawionego wykresu, jeżeli przedsiębiorstwo posiada zapas o łącznej wartości 120 000,00 zł?
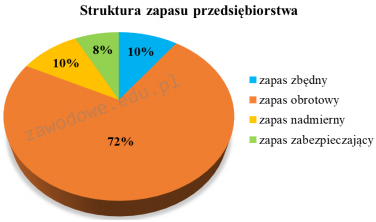
Wynik: 25/40 punktów (62,5%)
Wymagane minimum: 20 punktów (50%)
Ile wynosi wartość zapasu nieprawidłowego na podstawie przedstawionego wykresu, jeżeli przedsiębiorstwo posiada zapas o łącznej wartości 120 000,00 zł?
Ile minimum opakowań należy dostarczyć do magazynu, aby zrealizować zamówienie na 870 sztuk wiertarek?
Nazwa zapasu | Stan magazynowy [szt.] |
---|---|
Wiertarki w opakowaniu – gotowy towar | 110 |
Wiertarki | 1200 |
Obudowa wiertarki | 55 |
Opakowania | 200 |
Na podstawie danych z tabeli określ, w którym tygodniu pracownik magazynu miał największą wydajność w stosunku do wydajności planowanej.
Tydzień | A. | B. | C. | D. | |
---|---|---|---|---|---|
Wydajność w szt./h | planowana | 100 | 120 | 120 | 100 |
rzeczywista | 110 | 120 | 110 | 105 |
W magazynie przed przyjęciem znajdowało się 1 500 szt. towaru, a po przyjęciu 17 500 szt. Oblicz, jaka jest wartość średniego zapasu cyklicznego w tym magazynie, jeśli stanowi ona połowę wartości dostawy?
Opakowania klasyfikuje się w zależności od funkcji na:
Jak nazywa się zapas znajdujący się w systemie produkcyjnym podczas procesu obróbki?
W skład kosztów ryzyka związanych z magazynowaniem zapasów wchodzi
Znak towarowy umieszczony na opakowaniu informuje nas o maksymalnej
Podmioty ekonomiczne, które mają na celu zunifikowanie różnych usług logistycznych w jednym miejscu, przejmując część działań realizowanych przez macierzyste jednostki przedsiębiorstw - klientów, to
Który znak należy umieścić na opakowaniu biodegradowalnym?
Rodzajem środka transportu i manipulacji o ograniczonym zasięgu, który umożliwia przemieszczenie towarów zarówno w pionie, jak i poziomie, a także pod odpowiednim kątem, jest
W przypadku poważnych oparzeń, które prowadzą do martwicy, czyli całkowitego zniszczenia wszystkich warstw skóry (skóra jest poparzona, czarna lub biała), należy
Opłaty za przejazd samochodem po drogach krajowych uzależnione są między innymi od
W przypadku bezpośredniego kanału dystrybucji wyróżnia się związek
Wartość wskaźnika utrzymania powierzchni magazynowej wynosi 2 zł/m2. W kolejnym kwartale planuje się jego zwiększenie o 1 %. Jaką wartość osiągnie wskaźnik?
Korzystając z danych zawartych w tabelach, wskaż warunki przechowywania jaj w pomieszczeniach magazynowych.
Wymagania dotyczące wilgotności względnej powietrza podczas przechowywania towarów | |
---|---|
Optymalna wilgotność względna powietrza | Rodzaj towaru |
85 ÷ 90% | kwiaty, świeże owoce i warzywa, mrożonki owocowe i warzywne, ryby |
65 ÷ 80% | jaja, miód |
60 ÷ 70% | mąka, cukier, sól, zboże, suszone owoce, papier, drewno |
50% | żelazo, wyroby metalowe, deski |
Wymagania dotyczące temperatury powietrza podczas przechowywania towarów | |
---|---|
Temperatura przechowywania | Rodzaj towaru |
20°C | mąka, cukier, sól |
15°C | oleje jadalne, deski |
4°C ÷ 10°C | margaryna, mleko |
3°C ÷ 10°C | masło, smalec, jaja |
0°C ÷ 10°C | owoce, warzywa |
-18°C ÷ -26°C | mrożone mięso wieprzowe, drób, ryby |
Zgodnie z regułą priorytetu LIFO (Last In First Out) kolejność realizacji zadań jest następująca
Zadanie | Kolejność przyjęcia |
---|---|
a | 2 |
b | 4 |
c | 3 |
d | 1 |
Jakie będzie roczne ratio wydatków na utrzymanie powierzchni magazynowej, jeśli objętość użytkowa magazynu wynosi 2 500 m3, a jego powierzchnia użytkowa sięga 400 m2, przy rocznych kosztach magazynowania równych 280 000,00 zł?
Jaką wartość ma średni wskaźnik wykorzystania strefy składowania w magazynie o całkowitej objętości 8 760 m3, gdy strefa ta zajmuje 75% całkowitej powierzchni, a średni objętościowy ładunek wynosi 5 256 m3?
Jakie są wymiary palety typu EUR?
Który kod przedstawiono na rysunku opakowania?
Dokument wysyłkowy "Routing order" jest przesyłany zagranicznemu eksporterowi w celu zrealizowania wysyłki towaru importowanego, przy czym odpowiedzialność za transport spoczywa na kupującym. Ta zasada odnosi się do formuły handlowej oznaczonej skrótem
Ile wyniesie koszt transportu ładunku o masie 18 000 kg na dystansie 200 km, jeśli cena za tonokilometr wynosi 0,30 zł?
Jaką metodę wydawania towarów należy zastosować, jeżeli pierwsze w kolejności mają być wydawane towary, które najpóźniej dotarły?
Czym jest EDI?
Który wariant odpowiada właściwej kolejności etapów planowania dystrybucji w metodzie DRP (ang. Distribution Requirements Planning)?
|
|
A. | B. |
|
|
C. | D. |
Proces rozładowania środków transportu zewnętrznego, identyfikacja przesyłki, kontrola ilości i jakości towarów oraz ich rejestracja w stanach magazynowych to czynności realizowane w obszarze
Jakim skrótem określa się system informatyczny wykorzystywany do zarządzania w dystrybucji?
Przedstawiony na zdjęciu wózek widłowy stosuje się do przewożenia i podnoszenia ładunku
W tabeli przedstawiono odległości drogowe pomiędzy Warszawą, a wybranymi miastami Polski. Stawka za 1 km trasy wynosi 2,80 zł. Koszt całkowity przewozu towarów na trasie Warszawa - Poznań wynosi
Trasy | Odległości drogowe w km |
---|---|
Warszawa – Katowice – Kraków – Poznań – Wrocław | 295 293 308 351 |
Jedną z metod organizacji przestrzeni magazynowej jest
Do kategorii odpadów przemysłowych nie wlicza się
Badanie analizy ABC dotyczącej zapasów w magazynie w celu ich właściwego rozmieszczenia w strefie składowania, mającego na celu zredukowanie czasu operacji manipulacyjnych, realizowane jest na podstawie kryterium
Do zalet wprowadzenia systemu informatycznego do zarządzania magazynem (MSI) należy
Usytuowanie strefy przyjęć oraz wydań na przylegających do siebie ścianach strefy magazynowej określa układ
Oblicz roczną kwotę za przechowywanie 4 000 sztuk produktów, jeżeli jednostkowy roczny koszt ich magazynowania wynosi 40,00 zł, a marża zysku stosowana przez magazyn wynosi 30%
Wartość sprzedaży w firmie "Omega" w roku 2009 wyniosła 140 000 zł, natomiast w roku 2010 zwiększyła się do 175 000 zł, co stanowi 125% sprzedaży za rok 2009. Wskaźnik 125% jest przykładem
Jaki system informatyczny jest używany do zarządzania obiegiem zapasów w magazynach?
Koncepcja, w której systemowo ustala się potrzeby w zakresie dystrybucji oraz planuje popyt na gotowe wyroby, to
Przedsiębiorstwo pakuje wytwarzane wyroby do puszek stalowych. W ciągu jednego roku wprowadziło na rynek 248 ton opakowań stalowych. Korzystając z tabeli, w której zamieszczono fragment ustawy o gospodarce opakowaniami i odpadami opakowaniowymi ustal, ile kilogramów opakowań ze stali powinno przedsiębiorstwo poddać recyklingowi.
Ustawa z dnia 13 czerwca 2013 r. o gospodarce opakowaniami i odpadami opakowaniowymi | |||
Załącznik nr 1 docelowy poziom odzysku i recyklingu odpadów opakowaniowych | |||
Poz. | Odpady opakowaniowe powstałe z/ rodzaj opakowań | Poziom w % | |
odzysk | recykling | ||
1. | opakowań razem | 61 | 56 |
2. | opakowań z tworzyw sztucznych | – | 23,5 |
3. | opakowań z aluminium | – | 51 |
4. | opakowań ze stali, w tym z blachy stalowej | – | 51 |
5. | opakowań z papieru i tektury | – | 61 |
6. | opakowań ze szkła | – | 61 |
7. | opakowań z drewna | – | 16 |