Pytanie 1
Na rysunku przedstawiono
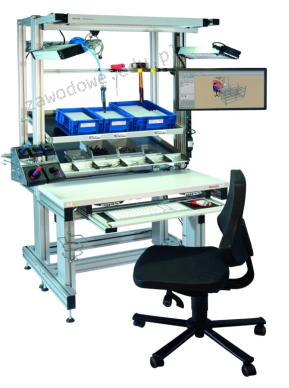
Wynik: 4/40 punktów (10,0%)
Wymagane minimum: 20 punktów (50%)
Na rysunku przedstawiono
Zakład odzieżowy otrzymał zamówienie na 1 000 sztuk ubrań dla dzieci. Aby uszyć jedną sztukę potrzebne jest 2,2 mb materiału. W magazynie dostępne jest 800 mb tkaniny. Ile metrów materiału trzeba zamówić, aby zrealizować to zamówienie?
W jakim typie obiektu magazynowego składowane jest paliwo ciekłe?
Gdy punkt, z którego realizowane jest zamówienie klienta, znajduje się w bliskiej odległości od klienta oraz rynku, to prawdopodobieństwo utraty zamówienia klienta
Aby ujednolicić oznaczenia na opakowaniach zbiorczych, wprowadzono etykietę logistyczną EAN-UCC. Jest to przykład
Przedstawiony znak oznacza materiały i przedmioty
Wykorzystanie strategii Just in Time (czyli dokładnie na czas) pozwala między innymi na zarządzanie
Który dokument powinien być wpisany na schemacie w miejscu oznaczonym znakiem zapytania?
Odzież ochronna, która musi być certyfikowana, to odzież
Jeśli wartość obrotu magazynowego w ciągu 14 dni wyniosła 1 200 500 kg towaru A oraz 2 800 ton towaru B, to jaki był średni dzienny obrót magazynowy?
Firma nabyła 40 t kruszywa w cenie 850,00 zł/t brutto przed przyznaniem rabatu. Jaka byłaby kwota, którą firma musiałaby uiścić za zakupione kruszywo, gdyby sprzedawca zaoferował jej rabat w wysokości 5%?
Informatyczny system wspomagający zarządzanie magazynami, obejmujący zarówno stany towarów, ich lokalizacje, jak również kierowanie i nadzorowanie działań realizowanych w magazynie oraz w interakcji z produkcją, przyjęciami, wysyłkami i innymi procesami, to system
Aby zabezpieczyć ładunek na palecie przed niekorzystnymi warunkami atmosferycznymi, należałoby użyć
Przeniesienie ładunku do pojazdu o mniejszej ładowności to
Jaką wartość miała dostawa do punktu sprzedaży detalicznej, jeżeli początkowy stan magazynowy wynosił 1 200 szt., sprzedaż wyniosła 900 szt., a końcowy stan to 500 szt.?
W kategorii Y analizy XYZ znajduje się oferta mająca charakter sezonowych fluktuacji
Brak odpowiedzi na to pytanie.
Stawka za godzinę pracy pracownika magazynu wynosi 12,00 zł, a koszt użytkowania wózka to 10,00 zł za 20 minut. Przewidywany czas na wyładunek środka transportu to 6 godzin. Jaki będzie łączny koszt wyładunku?
Brak odpowiedzi na to pytanie.
Do funkcji logistyki w obszarze dystrybucji przed dokonaniem transakcji nie zalicza się
Brak odpowiedzi na to pytanie.
Na którym rysunku przedstawiono zasieki magazynowe?
Brak odpowiedzi na to pytanie.
Ile jednostek ładunkowych paletowych (pjł) można utworzyć i zrealizować z magazynu w trakcie 5 dni, jeśli magazyn funkcjonuje w systemie dwóch zmian, a średnio w jednej zmianie przygotowywanych i wydawanych jest 220 pjł?
Brak odpowiedzi na to pytanie.
Na podstawie danych zamieszczonych w tabeli ustal, który dostawca nie zrealizował dostawy w uzgodnionym terminie.
Dostawca | Data otrzymania zamówienia | Uzgodniony termin realizacji dostawy | Data realizacji dostawy |
---|---|---|---|
A. | 01.06.2016 r. | 7 dni | 05.06.2016 r. |
B. | 12.05.2016 r. | 5 dni | 16.05.2016 r. |
C. | 24.06.2016 r. | 14 dni | 09.07.2016 r. |
D. | 25.05.2016 r. | 8 dni | 31.05.2016 r. |
Brak odpowiedzi na to pytanie.
W dniu 10.01.2020 r. wydano z magazynu na podstawie dokumentu WZ 1 400 sztuk zeszytów 60 kartkowych w kratkę. Na podstawie przedstawionej w tabeli ilościowo-wartościowej kartoteki magazynowej oblicz, ile zeszytów 60 kartkowych w kratkę zostało w magazynie po wydaniu.
ILOŚCIOWO-WARTOŚCIOWA KARTOTEKA MAGAZYNOWA | |||||||||
---|---|---|---|---|---|---|---|---|---|
Hurtownia PAPIEREK ul. Mickiewicza 11 75-004 Koszalin NIP 669-23-10-085 | Nazwa: zeszyt 60 kartkowy w kratkę Indeks: ZK/60 Jednostka miary: szt. | ||||||||
Lp. | Data | Symbol i nr dokumentu | Jednostkowa cena ewidencyjna [zł] | Ilość [szt.] | Wartość [zł] | ||||
Przychód | Rozchód | Zapas | Przychód | Rozchód | Zapas | ||||
1 | 02.01.2020 | PZ 1/2020 | 0,50 | 2 000 | – | 2 000 | 1 000,00 | – | 1 000,00 |
2 | 03.01.2020 | PZ 2/2020 | 0,45 | 2 500 | – | 4 500 | 1 125,00 | – | 2 125,00 |
3 | 08.01.2020 | WZ 14/2020 | 0,50 | - | 1 800 | 2 700 | - | 900,00 | 1 225,00 |
4 | 09.01.2020 | PZ 18/2020 | 0,55 | 1 500 | – | 4 200 | 825,00 | – | 2 050,00 |
Brak odpowiedzi na to pytanie.
Na rysunku przedstawiono
Brak odpowiedzi na to pytanie.
Jeśli strefa składowania ma długość 24 m, szerokość 4 m oraz powierzchnię zajmowaną przez towary wynoszącą 48 m2, to w jakim stopniu wykorzystana jest ta strefa składowania?
Brak odpowiedzi na to pytanie.
Firma logistyczna ma dostarczyć ładunek do czterech odbiorców, w kolejności: X, Y, Z, L jednym środkiem transportu. Czas dowozu zamówionego ładunku od dostawcy do odbiorcy X oraz powrót samochodu od odbiorcy L do bazy wynosi po 30 minut. Łączny czas pracy kierowcy wynosi
Trasa | Odległości | Prędkość pojazdu na trasie | Czas rozładunku |
---|---|---|---|
Odbiorca X-Y | 120 km | 60 km/h | 20 min. |
Odbiorca Y-Z | 60 km | 60 km/h | 20 min. |
Odbiorca Z-I | 180 km | 60 km/h | 20 min. |
Brak odpowiedzi na to pytanie.
W zakładzie zajmującym się produkcją napojów, surowce na linię produkcyjną z zbiorników magazynowych powinny być dostarczane przy pomocy
Brak odpowiedzi na to pytanie.
Przedstawiony harmonogram czasu pracy kierowców ilustruje liczbę kursów realizowanych przez przedsiębiorstwo logistyczne w ciągu dnia. Wyznacz trasę kierowcy IV zakładając, że każdy z kierowców spędza jednakową liczbę godzin za kierownicą.
Trasa -X- 220 km | Trasa -Y- 280 km | Trasa -Z- 160 km | Trasa -L- 340 km | Trasa -K- 440 km | Trasa -M- 440 km | Średnia prędkość pojazdu na trasie w km/h |
---|---|---|---|---|---|---|
Kierowca I | ——— | Kierowca I | Kierowca I | ——— | ——— | 80 |
——— | Kierowca II | ——— | ——— | Kierowca II | ——— | 80 |
Kierowca III | ——— | Kierowca III | Kierowca III | ——— | ——— | 80 |
——— | ——— | ——— | ——— | ——— | ——— | Kierowca IV |
Brak odpowiedzi na to pytanie.
W zakładzie szlifierskim przetwarzane są tuleje cylindryczne. Na wyprodukowanie 100 sztuk produktów potrzebne jest 192 roboczo-godzin. Ile dni roboczych należy zaplanować na wykonanie 100 sztuk tulei, jeśli dysponujemy 2 szlifierkami, a praca odbywa się na dwie zmiany po 8 godzin każda?
Brak odpowiedzi na to pytanie.
Który z podanych znaków należy umieścić na opakowaniu zbiorczym z tworzywa sztucznego, zawierającym serwisy kawowe z porcelany?
Brak odpowiedzi na to pytanie.
W której skrzyni można umieścić dokładnie 8 opakowań jednostkowych o wymiarach 0,5 x 0,5 x 0,5 m (dł. x szer. x wys.)?
Skrzynia | Długość [mm] | Szerokość [mm] | Wysokość [mm] |
---|---|---|---|
A. | 1 000 | 500 | 500 |
B. | 1 000 | 1 000 | 1 000 |
C. | 1 500 | 500 | 1 500 |
D. | 2 000 | 1 000 | 1 500 |
Brak odpowiedzi na to pytanie.
Do szkodników, które mają negatywny wpływ na przechowywane zapasy, zalicza się
Brak odpowiedzi na to pytanie.
Narzędzie do planowania, które precyzyjnie określa czas realizacji, datę rozpoczęcia oraz zakończenia działań podejmowanych przez pracowników jednostki organizacyjnej, nazywa się
Brak odpowiedzi na to pytanie.
W trakcie 8-godzinnej zmiany dwójka pracowników produkuje łącznie 32 drewniane podstawy do wieszaka. Oblicz, jaka jest norma czasu pracy na toczenie jednej podstawy.
Brak odpowiedzi na to pytanie.
Selekcja i pobieranie materiałów zgodnie z zamówieniami realizowane jest w obszarze
Brak odpowiedzi na to pytanie.
Do elementów wewnętrznych, które wpływają na wysokość kosztów logistyki w firmie, należą
Brak odpowiedzi na to pytanie.
Jak nazywa się system informatyczny, który łączy zarządzanie procesem produkcji z wykorzystaniem systemów typu CAx?
Brak odpowiedzi na to pytanie.
Czynność wykonywana w etapie magazynowania towarów to
Brak odpowiedzi na to pytanie.
Które towary zostały dostarczone niezgodnie z przedstawionym fragmentem wewnętrznej instrukcji przyjmowania towarów spożywczych do magazynu?
Fragment wewnętrznej instrukcji przyjmowania towarów spożywczych do magazynu | ||||
INSTRUKCJA PRZYJMOWANIA TOWARÓW SPOŻYWCZYCH DO MAGAZYNU Podczas dostawy towarów należy skontrolować:
Po sprawdzeniu wszystkich warunków należy wypełnić kartę przyjęcia towaru. | ||||
Nazwa towaru | Prawidłowe oznakowanie produktu* | Temperatura panująca w środku transportu | Rodzaj opakowania | Stan opakowania |
Lody | TAK/NIE | -20°C | karton | zamknięte i nieuszkodzone |
Jabłka | TAK/NIE | +3,5°C | skrzynia | nieuszkodzone |
Jogurty | TAK/NIE | -2,5°C | karton | zamknięte i nieuszkodzone |
Marmolada | TAK/NIE | +14°C | zgrzewka | nieuszkodzone |
* niepotrzebne skreślić |
Brak odpowiedzi na to pytanie.
Wyznacz optymalną wielkość dostawy, biorąc pod uwagę planowany roczny popyt na poziomie 40 000 sztuk, koszt realizacji jednego zamówienia wynoszący 500,00 zł, cenę jednostkową równą 100,00 zł oraz wskaźnik rocznego kosztu utrzymania zapasów wynoszący 0,1.
Brak odpowiedzi na to pytanie.
W strategii działania dystrybucji masowej, aby zapewnić dotarcie produktu do jak największej liczby konsumentów, stosuje się odpowiednie kanały dystrybucji
Brak odpowiedzi na to pytanie.