Pytanie 1
Poprawnie wypełniony druk zamówień w oparciu o zamieszczoną fakturę powinien zawierać informacje w pozycji
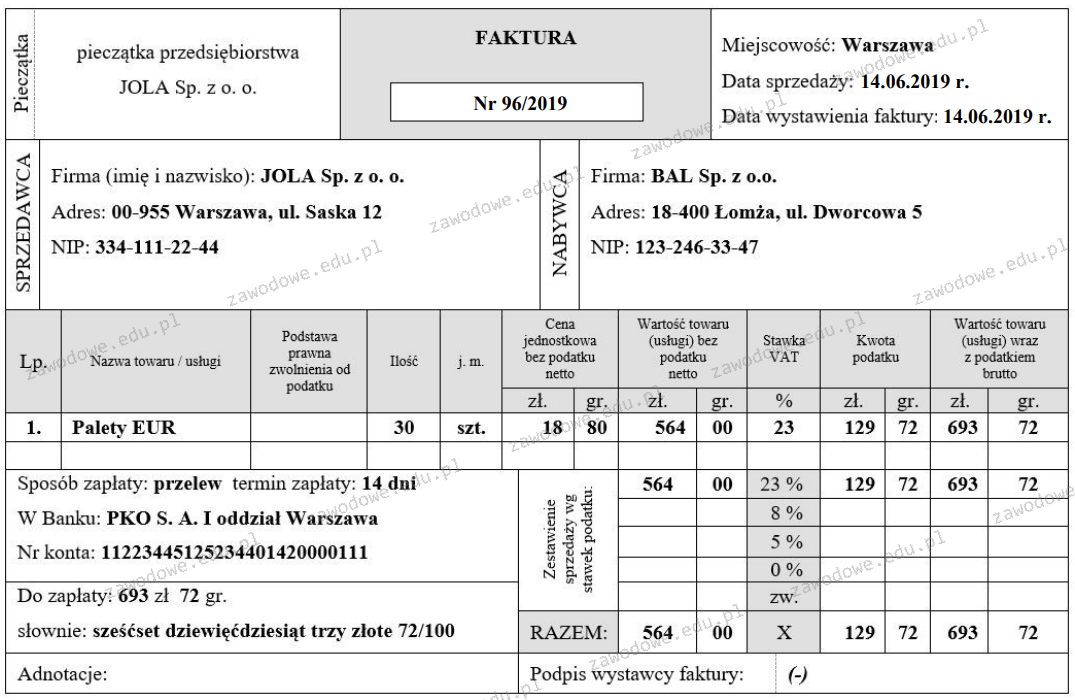
Wynik: 29/40 punktów (72,5%)
Wymagane minimum: 20 punktów (50%)
Poprawnie wypełniony druk zamówień w oparciu o zamieszczoną fakturę powinien zawierać informacje w pozycji
Masa pojedynczych elementów składanych ręcznie przez jednego pracownika, w przypadku pracy na stałym stanowisku, nie powinna być większa niż
Co oznacza termin MRP?
Czym jest strategia "Pull"?
Aby chronić się przed oczekiwanymi wzrostami cen, tworzy się zapas
Jakie będzie roczne ratio wydatków na utrzymanie powierzchni magazynowej, jeśli objętość użytkowa magazynu wynosi 2 500 m3, a jego powierzchnia użytkowa sięga 400 m2, przy rocznych kosztach magazynowania równych 280 000,00 zł?
Producent sprzętu kuchennego umieszcza je w kartonach, a następnie formuje w jednostki ładunkowe paletowe (pjł). Na każdej palecie roboty są rozmieszczane w 6 poziomach, a w każdym poziomie znajduje się 8 robotów. Ile pjł z robotami musi dostarczyć producent do hurtowni, która zamówiła 3 840 sztuk?
Firma otrzymała zlecenie na 200 paletowych jednostek ładunkowych skrzynek z napojami w szklanych butelkach. Skrzynki z napojami są układane na paletach w 7 poziomach, po 4 skrzynki w każdym poziomie. Ile butelek będzie potrzebnych do wykonania zamówienia, jeśli w jednej skrzynce znajduje się 24 butelki?
Jakie dokumenty magazynowe są tworzone w związku z przyjęciem do magazynu wyrobów gotowych z linii produkcyjnej?
Pojazd dostarczający 84 skrzyniopalety jabłek został podstawiony do rozładunku o godzinie 10:50. Wózek widłowy może zabrać 2 skrzyniopalety jednocześnie. Czas trwania jednego cyklu pracy wózka wynosi 3 minuty, przeprowadzenie kontroli jakościowej oraz ilościowej całej dostawy zajmuje 20 minut, a sporządzenie dokumentów przyjęcia dostawy trwa 15 minut. O której godzinie zakończy się przyjęcie jabłek do magazynu?
Wysoki poziom zapasów świeżych warzyw gromadzonych przez zakład przetwórczy stanowi zapas
Dokumentem transportowym, który stanowi dowód na zawarcie umowy spedycji, jest
Jakie są wymiary palety typu EUR?
Dostarczanie surowców bezpośrednio do miejsca produkcji, bez konieczności przechowywania zapasów, to podejście
Koszt utrzymania magazynu wynosi 4 zł/m2. Jaką kwotę trzeba będzie przeznaczyć na utrzymanie magazynu, jeśli w niedalekiej przyszłości planowany jest wzrost kosztów o 15%?
Na którym rysunku jest przedstawiony wózek podnośnikowy ręczny?
Aby magazyn mógł skutecznie pełnić swoje podstawowe zadanie, jakim jest przechowywanie zapasów, najwięcej miejsca powinno zajmować
W trakcie załadunku ciężarówki u pracownika wystąpiło zamknięte złamanie kończyny dolnej. Jak powinna wyglądać pierwsza pomoc w tej sytuacji?
W obszarze funkcji potransakcyjnych w systemie dystrybucji mieszczą się
Wartość brutto sprzedanych towarów zgodnie z przedstawioną fakturą wynosi
W metodzie MRP, ilość wymaganych materiałów ustalana jest na podstawie
Jak obliczyć procent wykorzystania powierzchni składowej magazynu, który jest przystosowany do przechowywania 20 000 paletowych jednostek ładunkowych (pjł), gdy średnia liczba składowanych pjł wynosi 15 000?
Złożone operacje logistyczne wymagają przeprowadzenia analizy strategicznej dotyczącej transportu. Na podstawie uzyskanych danych podejmowane są decyzje?
Jak nazywa się proces, w którym owoce tracą wodę podczas przechowywania w magazynie?
Procesy umożliwiające całkowite lub częściowe wykorzystanie odpadów, które prowadzą do odzyskania zawartych w nich substancji, materiałów lub energii bez stwarzania zagrożenia dla zdrowia i życia, to
Analiza zadowolenia klientów z wprowadzonej usługi należy do działań
Harmonogramy dostaw surowców w firmie produkcyjnej są ustalane na podstawie efektywności łańcucha dostaw, który określa zdolności sprzedażowe jakiegokolwiek produktu, liczone na poziomie
Operacje takie jak rozładunek zewnętrznych środków transportu, sortowanie, identyfikacja oraz kontrola ilościowa i jakościowa towarów są realizowane w obszarze
Jakie jest określenie systemu zamawiania produktów, który opiera się na formule ustalenia wielkości partii dostawy jako różnicy pomiędzy maksymalnym poziomem zapasu a aktualnym stanem zapasu, oraz na przygotowaniu zamówienia w ustalonym cyklu, gdy bieżący stan zapasu jest niższy od zdefiniowanego minimum?
Firma zajmująca się produkcją wykorzystuje technologie produkcji opakowań zwrotnych, które oszczędzają materiały. Zakres działań, które podjęła w celu ochrony środowiska, obejmuje
Całkowite wydatki na przechowywanie towarów w danym czasie wyniosły 8 000 zł, a wartość obrotu magazynowego obliczona na podstawie rozchodu osiągnęła 2 000 szt. Jaki jest koszt jednostkowy przechowywania towarów?
W zakładzie szlifierskim przetwarzane są tuleje cylindryczne. Na wyprodukowanie 100 sztuk produktów potrzebne jest 192 roboczo-godzin. Ile dni roboczych należy zaplanować na wykonanie 100 sztuk tulei, jeśli dysponujemy 2 szlifierkami, a praca odbywa się na dwie zmiany po 8 godzin każda?
Który z podanych czynników nie jest wprost związany z opracowywaniem wielkości zaopatrzenia materiałowego?
Jakim prefiksem posługuje się system kodów kreskowych EAN w Polsce?
Jaką kwotę należy zapłacić spedytorowi morskiemu w przypadku, gdy obsłuży on 2 kontenery 40' oraz 3 kontenery 20', przy stawce 100 USD/TEU (20-stopowa jednostka przeliczeniowa)?
Które przedsiębiorstwo transportowe powinno wybrać centrum dystrybucyjne do dystrybucji ładunku na odległość 100 km, uwzględniając informacje zawarte w tabeli oraz hierarchię kryteriów - dostarczenie towaru po najniższym koszcie i w czasie nie dłuższym niż 2 godziny 15 minut?
Przedsiębiorstwo transportowe | Średnia prędkość samochodów, km/h | Koszt, zł/1 km |
---|---|---|
A. | 40 | 2,00 |
B. | 45 | 2,50 |
C. | 50 | 3,00 |
D. | 55 | 3,50 |
Termin "szybkiej reakcji" w logistyce obsługi klienta oznacza
Jakie są negatywne aspekty transportu drogowego?
To pytanie jest dostępne tylko dla zalogowanych użytkowników. Zaloguj się lub utwórz konto aby zobaczyć pełną treść pytania.
Odpowiedzi dostępne po zalogowaniu.
Wyjaśnienie dostępne po zalogowaniu.
To pytanie jest dostępne tylko dla zalogowanych użytkowników. Zaloguj się lub utwórz konto aby zobaczyć pełną treść pytania.
Odpowiedzi dostępne po zalogowaniu.
Wyjaśnienie dostępne po zalogowaniu.